Are you curious why the world’s leading companies like Mercedes and Rolls-Royce invest heavily in axial flux motors? As a professional axial flux motor core manufacturer in China, we’ve spent years perfecting these advanced motors.
Today, we’re here to share our insights on why are axial flux motors considered the future of electric vehicles. From their unique motor design to their impressive performance in electric vehicles and aerospace, we’ll explain everything you need to know. Let’s dive in.
What is an Axial Flux Motor?
Axial flux motors differ from radial flux motors primarily in the direction of their magnetic flux path. While both types operate on the same electromagnetic principles, the key difference lies in how the magnetic field interacts with the rotor and stator.
In an axial flux motor, the stator’s magnetic poles are arranged along the axis, with the rotor typically shaped like a cylinder. The magnetic flux passes through the rotor’s central axis. When current flows through the stator windings, it generates a magnetic field that travels along the axial direction through the rotor. According to Lorentz’s law, this magnetic field creates torque within the rotor, causing it to spin.
Axial flux motors are often disc-shaped with a planar air gap and short axial length, earning them the nickname “disc motors.”
Topology of Axial Flux Motor
The topology of axial flux motors is highly flexible, allowing for customization based on specific application needs. There are four primary configurations:
Single Stator/Single Rotor:
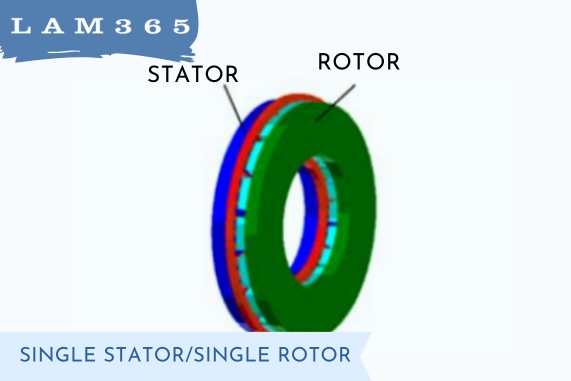
This setup has one stator and one rotor, offering a compact design but with high unbalanced magnetic pull, leading to increased bearing load, vibration, noise, and potential friction between the stator and rotor, which can shorten the motor’s lifespan.
Single Stator/Dual Rotor:
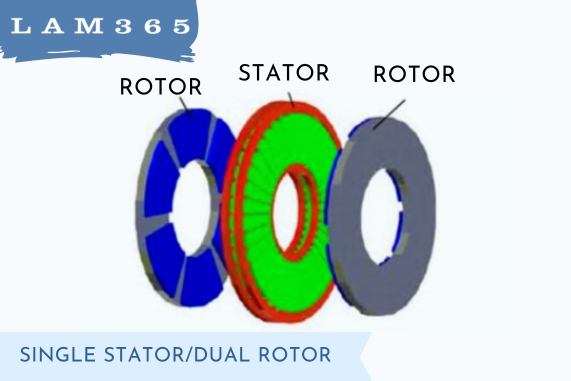
This features two external stators and one internal rotor, providing high power density, and making it ideal for traction systems and aerospace applications.
Dual Stator/Single Rotor:
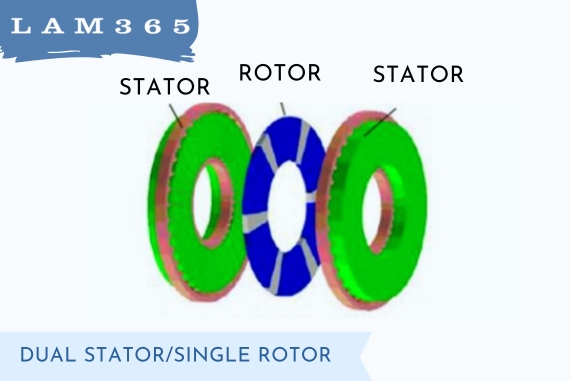
With two external rotors and one internal stator, this symmetric design reduces unbalanced magnetic pull, suitable for wind power systems.
Multi-Stator/Multi-Rotor:
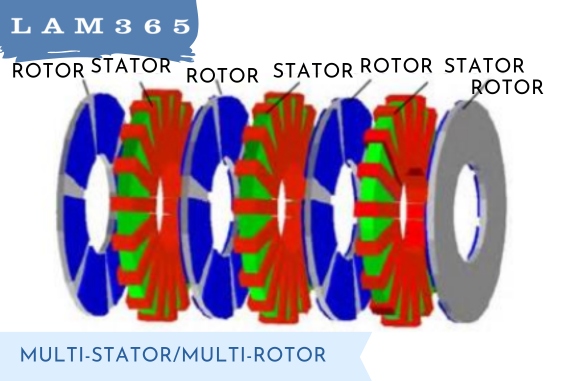
Designed for high-torque applications, such as marine propulsion and large-scale wind and hydro generators.
Advantages of Axial Flux Motors
Axial flux technology offers several significant advantages:
1. Compact Size and Lightweight Design:
Pioneered by YASA, axial flux electric motors are about half the size and weight of traditional radial flux motors.
YASA AXIAL MOTOR | Radial MOTOR | |
Volume | 5 | 10 |
Quality | 24 | 50 |
Torque | 800 | 400 |
Power | 358 | 186 |
Torque density | 160 | 40 |
Power density | 14.9 | 3.7 |
For example, YASA’s axial flux motor has a volume of 5L and weighs 24kg, compared to a typical automotive radial motor’s 10L and 50kg.
This makes axial flux motors ideal for the automotive industry’s push toward lightweight, offering greater installation flexibility due to their shorter radial length.
2. High Torque and Power Density:
Axial flux motors achieve higher torque and power density because the effective magnetic surface area is on the rotor’s surface, not the outer diameter.
YASA’s motors deliver a torque density of 160Nm/L and a power density of 14.9kW/kg—four times that of conventional radial motors.
3. High Efficiency:
With a shorter one-dimensional magnetic flux path, axial flux motors achieve efficiency levels of over 96%, outperforming many radial motors. They also save 15-25% more energy across power ranges and sustain peak power output longer.
4. Low Noise and Vibration:
The even magnetic field distribution results in quieter and smoother operation, making axial flux motors suitable for noise-sensitive applications.
5. Energy Saving and Carbon Reduction:
The compact design and lightweight materials reduce copper, iron, and magnet consumption by about 50% compared to radial motors, further lowered by coreless PCB stator technology. Their efficiency also means lower energy consumption, contributing to energy savings and carbon reduction.
Limitations of Axial Flux Technology
Axial flux motors, while highly efficient, come with certain limitations:
1. Cost Issues:
The specialized materials and manufacturing processes required for axial flux motors make them more expensive than traditional radial flux motors. For instance, using yoke-free topologies and unique stator-rotor designs can significantly increase production costs.
2. Design and Production Complexity:
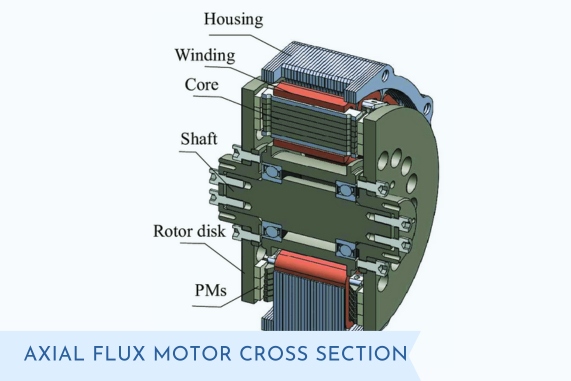
Designing and producing axial flux motors is more complex, particularly in maintaining uniform air gaps between the rotor and stator. The axial force during operation can exert a considerable pull on the motor shaft. Additionally, the manufacturing techniques and machinery are less mature compared to radial motors, limiting large-scale production.
3. Cooling Challenges:
The windings in axial flux motors are positioned deep within the stator and between the rotor discs, making heat dissipation difficult. This can lead to overheating during high-load operations, impacting motor performance and longevity.
Applications of Axial Flux Motors
Axial flux motors are widely used in various high-torque, compact-space applications such as electric vehicles, aerospace, marine propulsion, robotics, and wind power generation.
1. Electric Vehicles:
Axial flux motors’ compact size and low theoretical cost make them ideal for overcoming the challenges of in-wheel motors, supporting their large-scale adoption. Their high power density ensures sufficient torque output while maintaining lightweight, contributing to the mass production of hub motors. According to global information estimates, by 2027, the global automotive axial motor market will rise from $135 million in 2022 to $497 million, with a CAGR of 29.8%.
2. Aerospace:
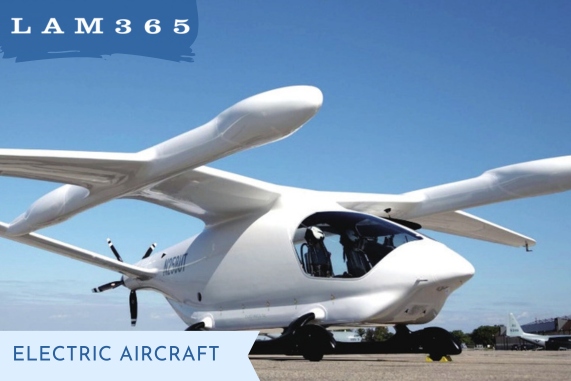
In 2021, the “Spirit of Innovation” in the ACCEL project was born, setting a pure electric aircraft airspeed record of 345.4 MPH. The fixed-wing aircraft is equipped with an axial motor with a propulsion power of 400KW.
Industry energy estimates that the urban air mobility market alone will grow to more than $100 billion by 2035. According to M&M estimates, the aircraft motor market size will grow from $8.2 billion in 2022 to $12.9 billion in 2027, with a compound annual growth rate of 9.4%.
Among them, axial motors with 5-10kW/kg power density will occupy the largest market share during the forecast period.
3. Marine Propulsion:
Axial flux motors offer significant advantages in efficiency, emission reduction, and structural optimization for ships. Saietta’s Propel S1 outboard motor, utilizing the AFT 140 axial motor, achieves an overall efficiency of 62%.
4. Robotics:
High-end robotics demand motors with quick response times, high torque-to-inertia ratios, and compact designs. Axial flux motors excel in providing high peak torque and rapid response in minimal space, as demonstrated by Genesis Robotics’ LiveDrive motor with its compact 2cm thickness. The mobile robotics components market is expected to grow rapidly, with a projected CAGR of 44.8%, reaching $7.4 billion by 2027.
Conclusion
Axial flux motors are revolutionizing industries with their compact size, high efficiency, and superior torque density. Whether in electric vehicles, aerospace, marine propulsion, or robotics, these motors are setting new standards for performance and sustainability. As a seasoned manufacturer of axial flux motor cores, we understand the unique advantages and challenges of this technology.
Ready to take your project to the next level with custom axial flux motor cores? Contact us today to discuss how we can help you achieve your goals with precision-engineered solutions tailored to your specific needs.