Rotor Die Casting in China
As a leading motor lamination stacks manufacturer in China, we specialize in producing various motor cores for a wide range of motors. We also provide centrifugal casting and aluminum die casting services for rotor stacks, ensuring high precision, durability, and performance.
Aluminum Die Casting Mold Design & Maintainability
Using CAD software, our engineers create detailed mold designs that ensure optimal flow, minimal defects, and high-quality rotor production.
And we can manufacture single and multiple cavity casting dies. Each mold is crafted from high-grade tungsten steel materials to withstand the rigors of high-pressure casting, ensuring longevity and consistent performance.
To maintain peak efficiency, we implement a robust mold maintenance program. This includes regular inspections, thorough cleaning, and timely repairs to prevent wear and extend mold life.
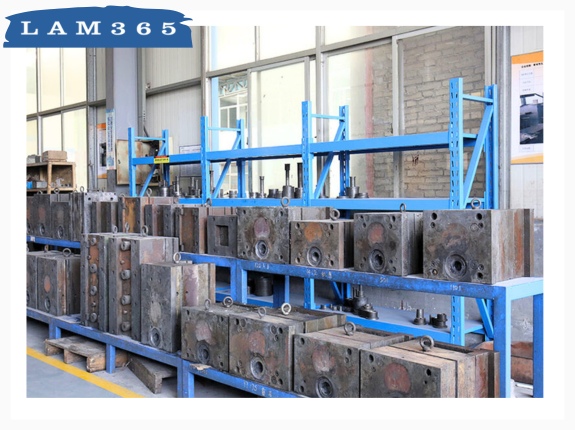
Die Casting Process for Rotors
Lam365 manufactures various die cast rotor cores to meet customer specifications. We have horizontal cold high-pressure die casting machines of capacity 280T and 400T and advanced four and six-processing station centrifugal casting machines.
The die casting process for rotors incorporates advanced techniques such as squeeze casting and centrifugal casting to ensure optimal performance and quality.

Squeeze Casting
This method involves injecting molten aluminum into a preheated mold under high pressure. The pressure is maintained during the solidification phase, resulting in a dense, high-strength rotor with minimal porosity and superior mechanical properties.
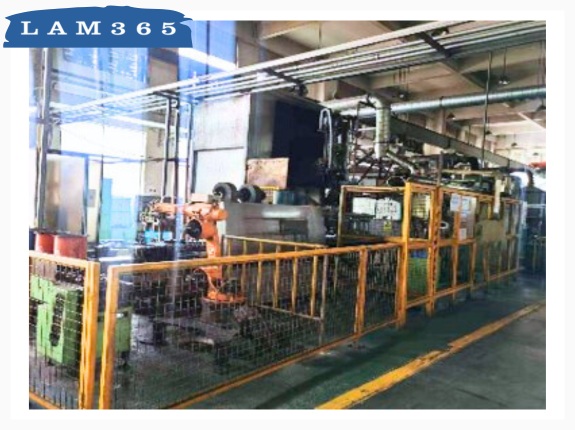
Centrifugal Casting
In this technique, molten aluminum is poured into a rotating mold. The centrifugal force distributes the metal uniformly, ensuring a consistent and defect-free rotor. This method is ideal for producing rotors with excellent dimensional accuracy and structural integrity.
Features of Aluminum Die Casting Rotor Cores
Lam365 manufactures various die cast rotor cores to meet customer specifications. We have horizontal cold high-pressure die casting machines of capacity 280T and 400T and advanced four and six-processing station centrifugal casting machines.
The die casting process for rotors incorporates advanced techniques such as squeeze casting and centrifugal casting to ensure optimal performance and quality.
Lightweight
Reduces overall motor weight, enhancing efficiency.
High Power-to-Mass Density
Improves motor performance and energy efficiency.
Low Moment of Inertia
Enables quicker acceleration and deceleration.
Greater Starting Torque
Provides robust initial power for various applications.
Low Manufacturing Cost
The mature manufacturing process reduce production expenses.
Enhanced Durability
Aluminum’s properties ensure long-lasting, reliable rotors.
FAQs
Copper rotors offer higher electrical conductivity and efficiency but are heavier and more expensive to produce.
Aluminum rotors are lighter, more cost-effective, and have a mature manufacturing process, making them ideal for applications requiring lower weight and cost.
Both materials provide specific benefits depending on performance and budget requirements.
Die-cast rotors are suitable for various types of motors, particularly squirrel-cage induction motors. They are widely used in new energy vehicles, industrial machinery, and consumer electronics.
Their lightweight, high power-to-mass density, and cost-effectiveness make them ideal for applications requiring efficient, durable, and high-performance motors.
Centrifugal casting and die casting are both methods for producing aluminum components. But they differ significantly.
Centrifugal casting involves pouring molten aluminum into a rotating mold, utilizing centrifugal force to achieve uniform density and minimal defects, ideal for cylindrical parts.
Die casting injects molten aluminum into a high-pressure mold, producing complex shapes with high precision and smooth finishes.
Centrifugal casting excels in structural integrity, while die casting offers higher production efficiency and intricate detailing.
You need to choose based on specific application needs.
Ready to manufacture rotor lamination stacks in China?
Ready to discuss die cast rotor lamination stacks with our China team? Contact us today to explore how our expertise and advanced manufacturing capabilities can meet your needs. Let’s create high-performance solutions for your projects!
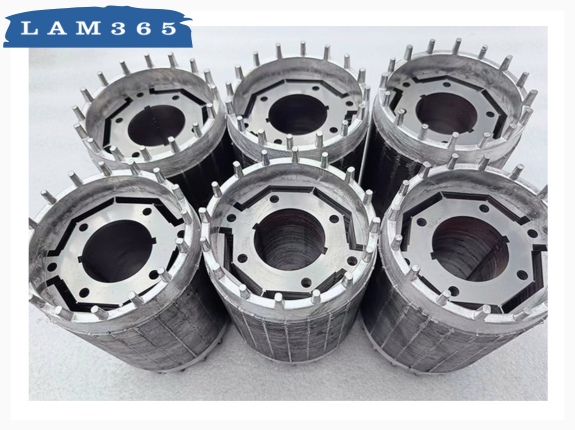