Glue Bonding Lamination Stacks in China
Without Interlocking and Laser Welding and Riveting
Glue bonding lamination stacks are one of our core competencies in manufacturing high-performance motor cores. By using specialized adhesives, we ensure that each layer of the lamination stack is securely bonded, resulting in improved electrical insulation, reduced vibrations, and enhanced overall motor efficiency.
Suitable for new energy vehicle motors, coreless motors, drone motors, robot motors. We also provide self-bonding motor cores.
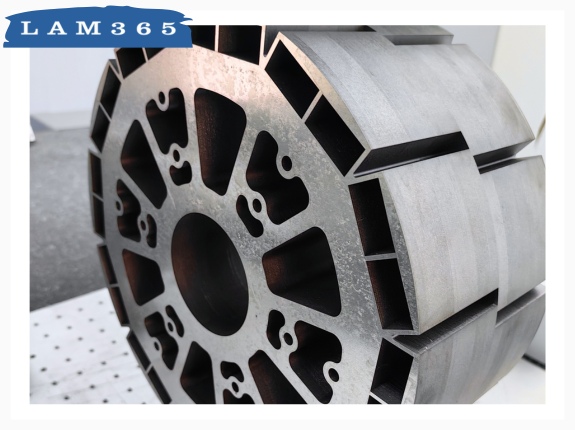
Manufacturing process of Glue Bonding
The best alternative to laser welded stacking is adhesive lamination. Adhesive reduces interlayer losses and corrosion. It improves thermal conductivity, reduces buzzing noise and improves resistance to high temperatures.
The process of stator and rotor lamination glue bonding involves several precise steps to ensure optimal performance and durability. Here is an overview of our glue bonding process:
4. Custom Fixtures
Once the laminations have cooled and can be handled, they are stacked into custom fixtures. These fixtures are designed to precisely compress the laminations, ensuring they are aligned correctly and uniformly.
5. Furnace Heating
The stacked fixtures are then placed in a furnace for final curing. This heating process ensures the bonding agent reaches its final Class C stage, providing maximum strength and durability.
6. Quality Inspection
Each bonded motor core is examined to ensure it meets our stringent quality standards. This includes checking for proper bonding, alignment, and overall integrity of the lamination stack.
1. Stamping or Laser Cutting Electrical Steel Sheets
The first step involves cutting the electrical steel sheets to the required shape and size. This is done using high-precision stamping or laser cutting techniques to ensure each lamination is accurately formed.
2. Applying Bonding Adhesive
Next, the bonding adhesive is applied to the steel sheets. This can be done using a roll coating process or a dip tank process or hand gluing.
3. Curing
The adhesive-coated laminations are then cured to a Class B stage. This initial curing step ensures that the adhesive begins to set and bond to the steel sheets, providing a preliminary bond that allows the laminations to be handled for further processing.
Glue Bonding Lamination Stacks Products
Lamination bonding is designed for high-efficiency electric powertrain applications. We specialize in manufacturing various motor cores using this advanced stacking technology. Our product range includes segmented motor cores, coreless motor cores, and EV motor cores, and more. All are bonded with precision for optimal performance. We can offer custom solutions for motor stator and rotor lamination stacks, tailored to meet your specific requirements.
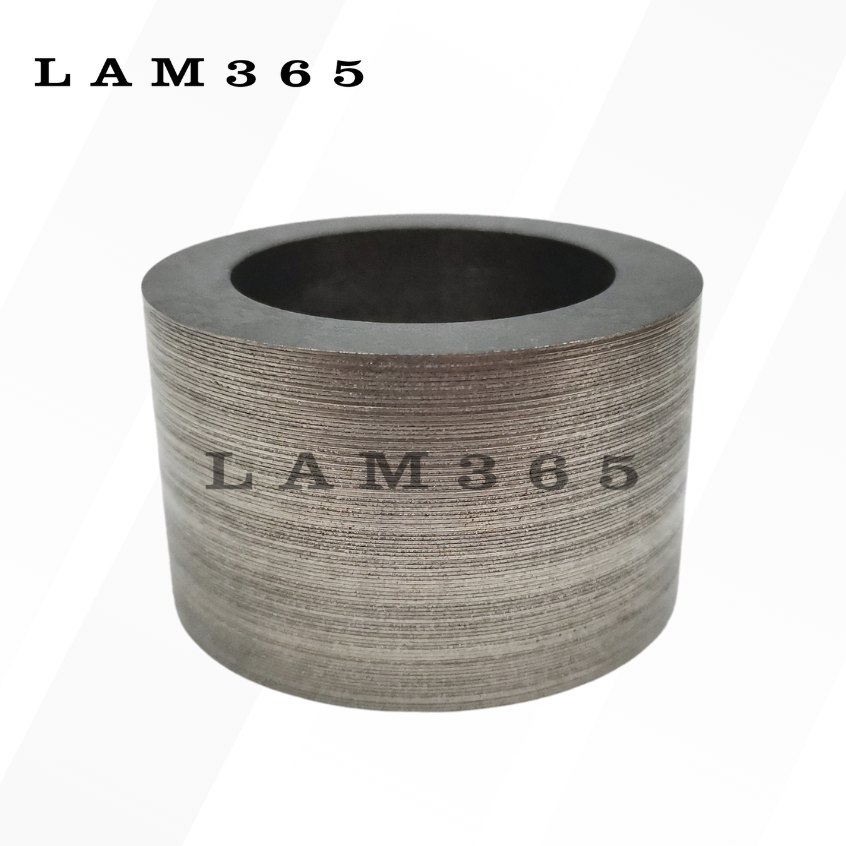
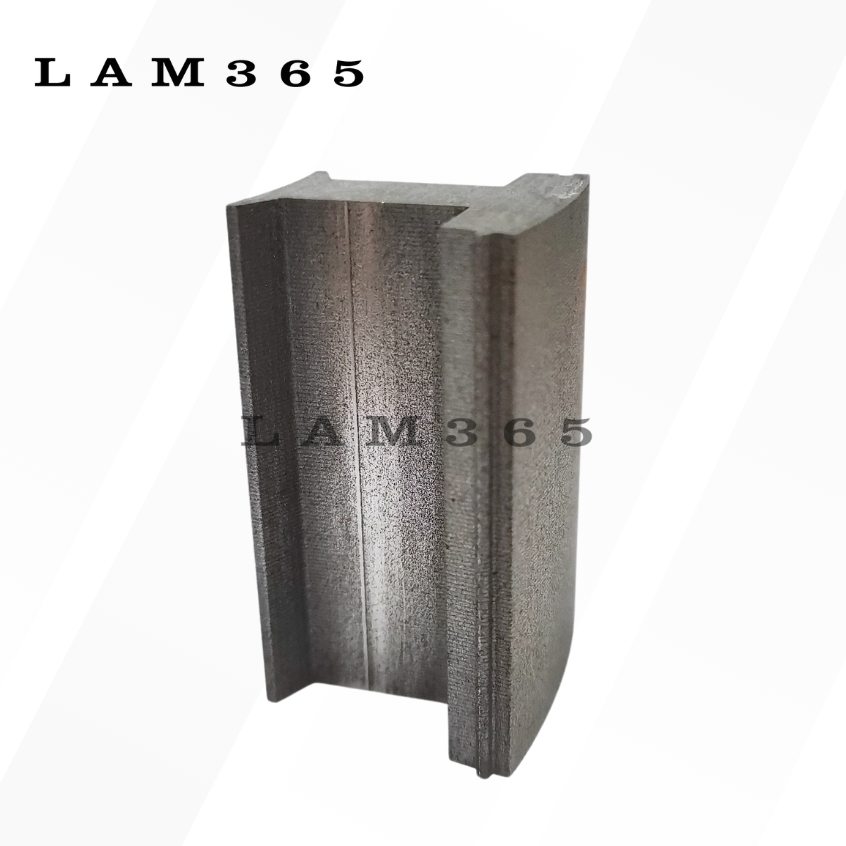
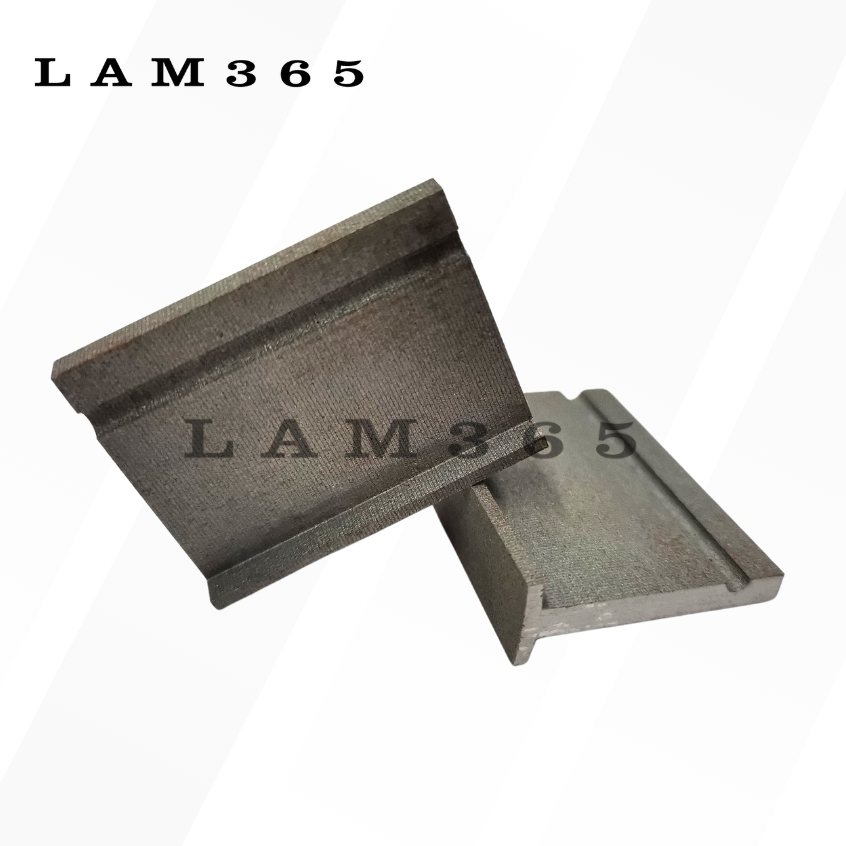
Benefits of Glue Bonding for Lamination Stacks
Increased Power Density
By ensuring a precise and uniform bond, glue bonding helps maximize the power density of the motor cores, allowing for more efficient energy usage and improved performance.
Reduced Vibration and Noise
The bonding process reduces vibrations and noise during motor operations, resulting in quieter and smoother performance.
Great Thermal Conductivity
Glue bonded laminations exhibit excellent thermal conductivity, which helps dissipate heat more effectively, maintaining optimal operating temperatures.
Conventional stacking techniques for electrical steel lamination stacks
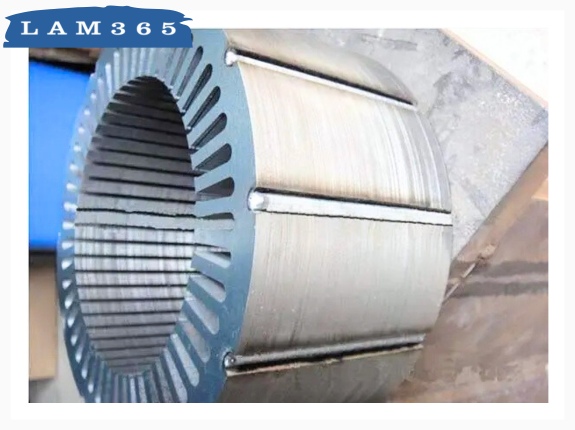
Laser welding
This technique uses a high-powered laser to weld the laminations together at specific points. Laser welding provides a strong bond and precise alignment but can introduce localized heating.
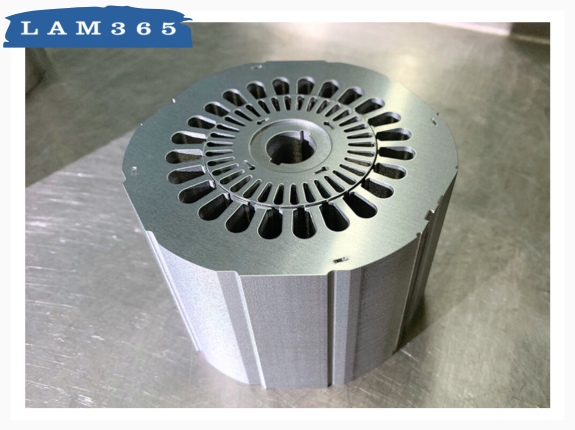
Interlocking
Interlocking involves creating tabs and slots on the edges of the laminations, allowing them to snap together without the need for additional bonding agents.
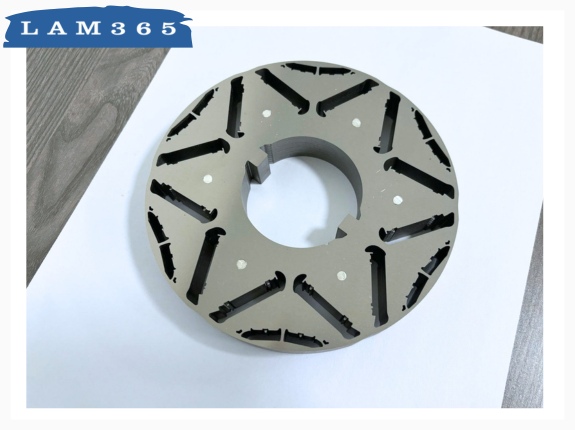
Riveting
Riveting uses mechanical fasteners to hold the laminations together. This method is reliable and easy to implement but can add weight and create stress points within the stack.
FAQs
Bonding varnish offers several advantages over traditional methods like welding or riveting. It provides a seamless connection, reducing the need for bulky mechanical fasteners, which results in lighter and more compact motor designs.
Additionally, backlack ensures even stress distribution across the bond area, enhancing the durability and performance of the motor by preventing localized pressure points and reducing vibration and noise.
No, glue bonding is generally more suitable for prototyping and small-scale production rather than high-volume production. While glue bonding provides precise and robust adhesion, the process can be time-consuming and less efficient for large-scale manufacturing.
The curing times and careful application required for glue bonding can lead to slower production speeds compared to other methods like laser welding or mechanical fastening.
Adhesive bonding technology plays a crucial role in the manufacturing of motors for new energy vehicles (NEVs), such as electric vehicles (EVs) and hybrid electric vehicles (HEVs). It enhances efficiency and performance by providing a uniform bond that reduces energy losses and improves thermal management.
It also reduces noise and vibration, allowing for quieter operation. This technology supports lightweight, compact designs and offers durability against environmental factors, crucial for extending motor lifespan.
Contact Us for Your Glue Bonding Needs
If you’re looking for high-quality glue bonding lamination stacks for your motor cores, we are here to help. Our expertise in manufacturing and advanced bonding technology ensures superior performance and reliability for your applications.
Contact us today to discuss your specific requirements and get a customized solution. Reach out via phone or email, or use our online inquiry form. Let us provide you with the best glue bonding solutions for your motor manufacturing needs.