Motor Stator Lamination Stacks in China
As a leading custom stator lamination stacks manufacturer in China, we specialize in customizing various stator cores for various motors, including BLDC motors, PMSM motors, stepper motors, and servo motors. All laminations are made from high-quality electrical steel of 0.1 to 0.5 mm in thickness. We offer products in the form of stator laminations and assembled stator stacks.
Our stator lamination stacks across multiple industries, serving sectors such as electric vehicles, drones, industrial machinery, and robotics. Contact us for prototype stator cores or high-volume motor stators.
Customize Different Types of Stator Cores
By laser cutting or wire cutting, we can quickly make the prototype of stator lamination. The minimum order quantity is even 1. With high speed progressive stamping tools, we can produce individual laminations or join them into stator stacks already in the stamping process using the technology of interlocking clamps in the mold.
We offer a wide range of customization options for different types of stator cores to meet the unique needs of various motor applications. Our capabilities include:
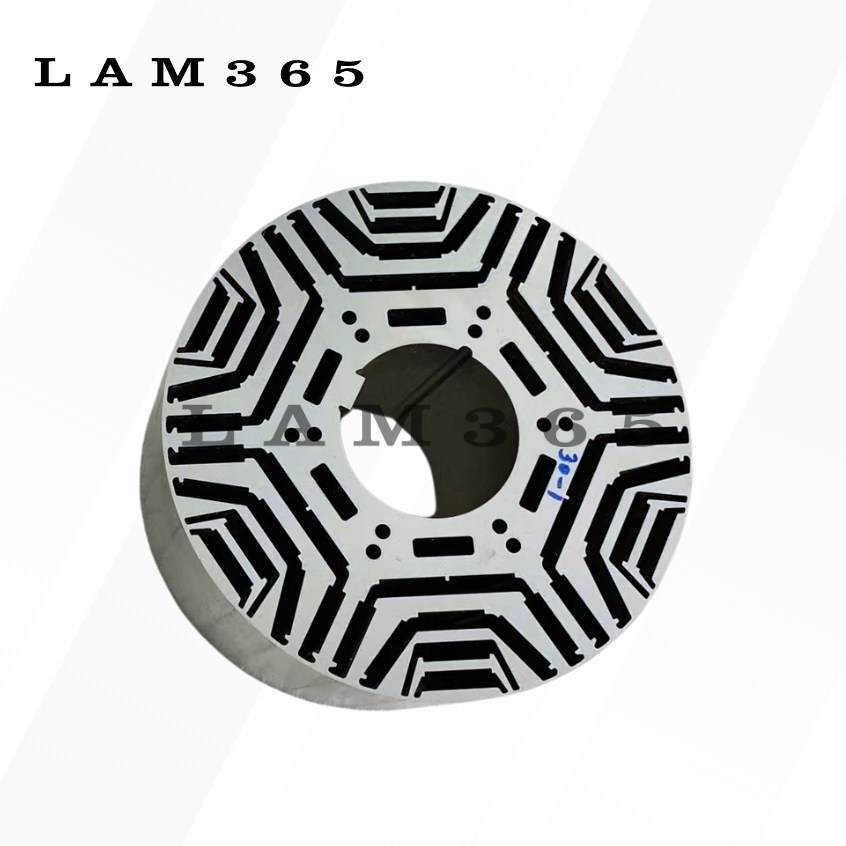
Innovative self-bonding technology enhances mechanical stability and magnetic performance, making them ideal for EV applications.
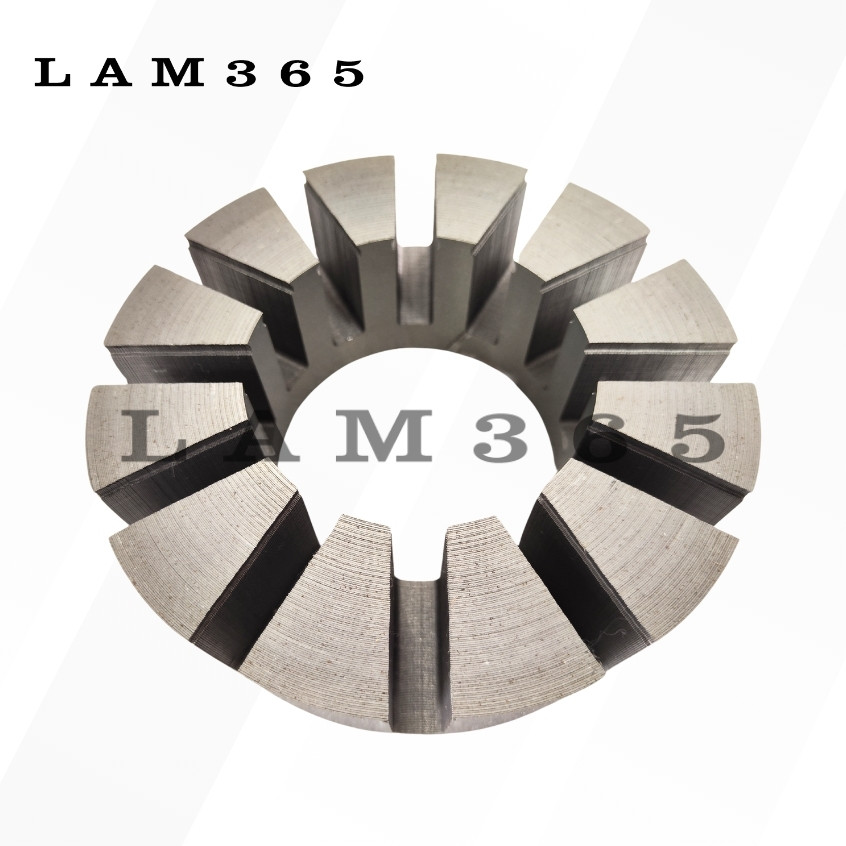
Optimized for high power density and efficiency, suitable for compact and lightweight designs.
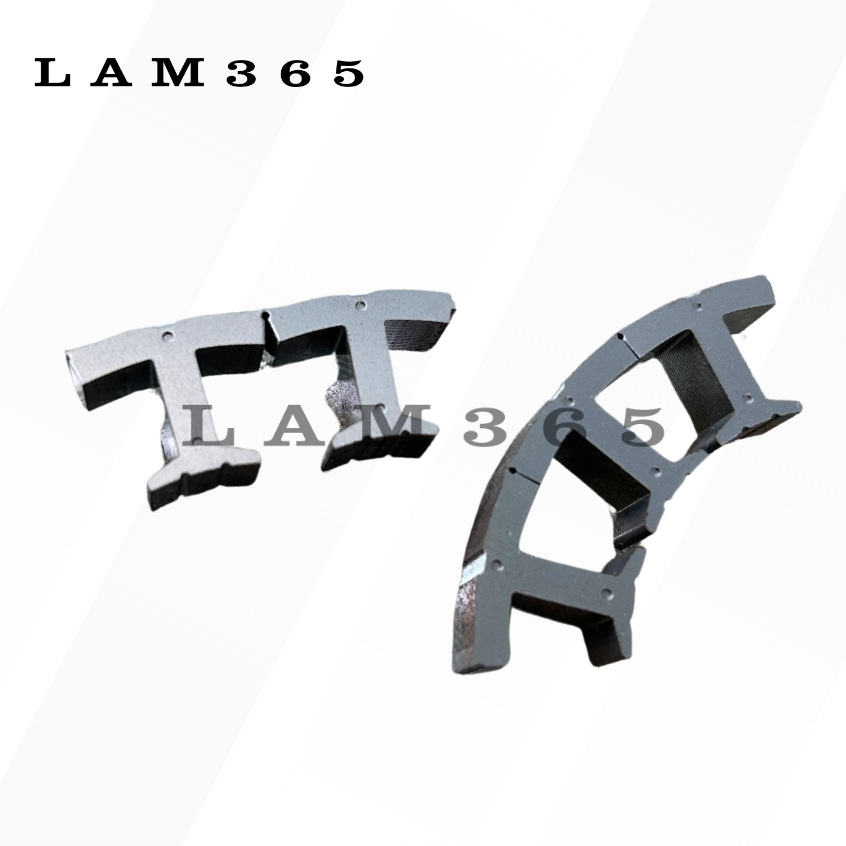
Segmented Stator Laminations
Allow for easier assembly and better thermal management, suitable for large motors.
Types of Electric Motor Stator Core Lamination
We specialize in customizing a variety of electric motor stator core laminations to suit diverse applications:
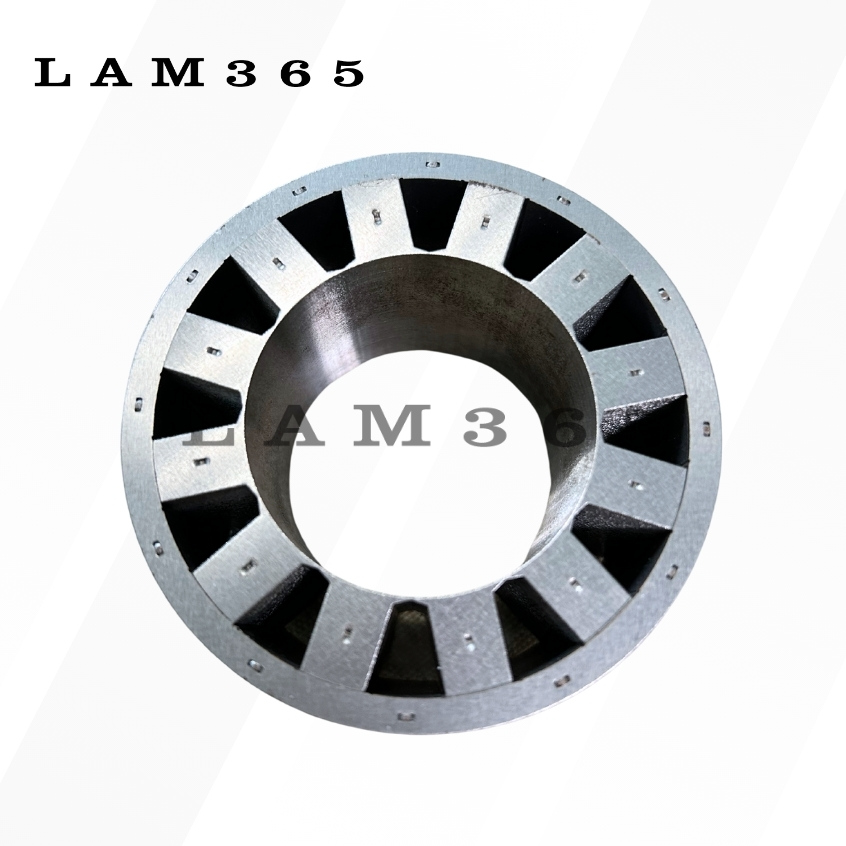
PMSM Motor Stator Core
Custom laminations for permanent magnet synchronous motors, enhancing efficiency and power output.
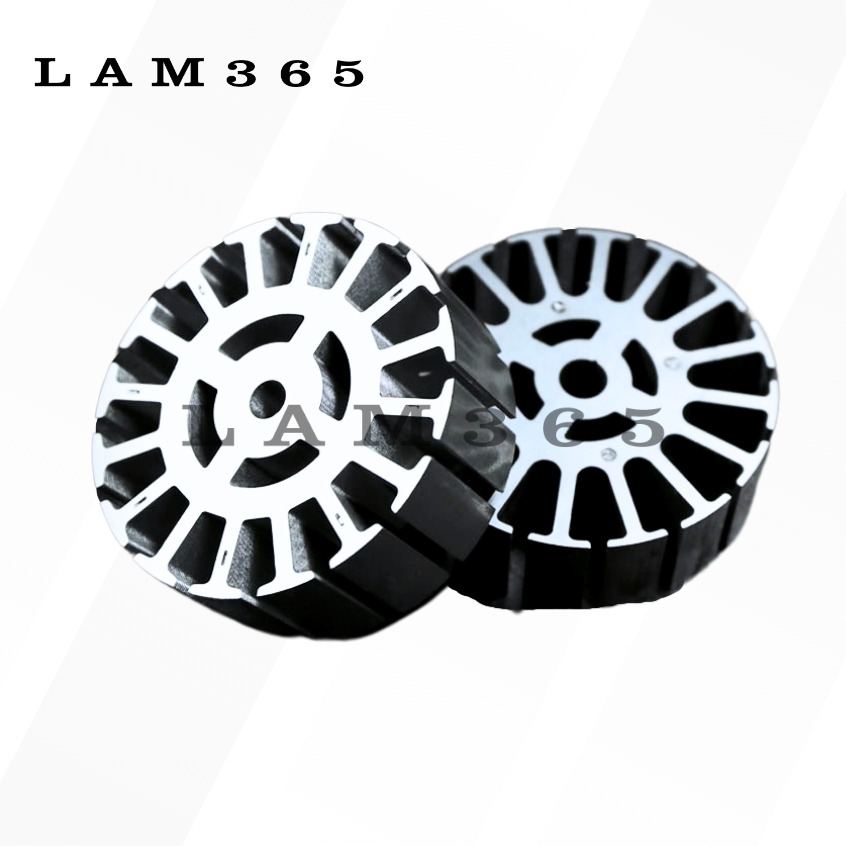
BLDC Motor Stator Core
Engineered for brushless DC motors, providing superior performance and durability.
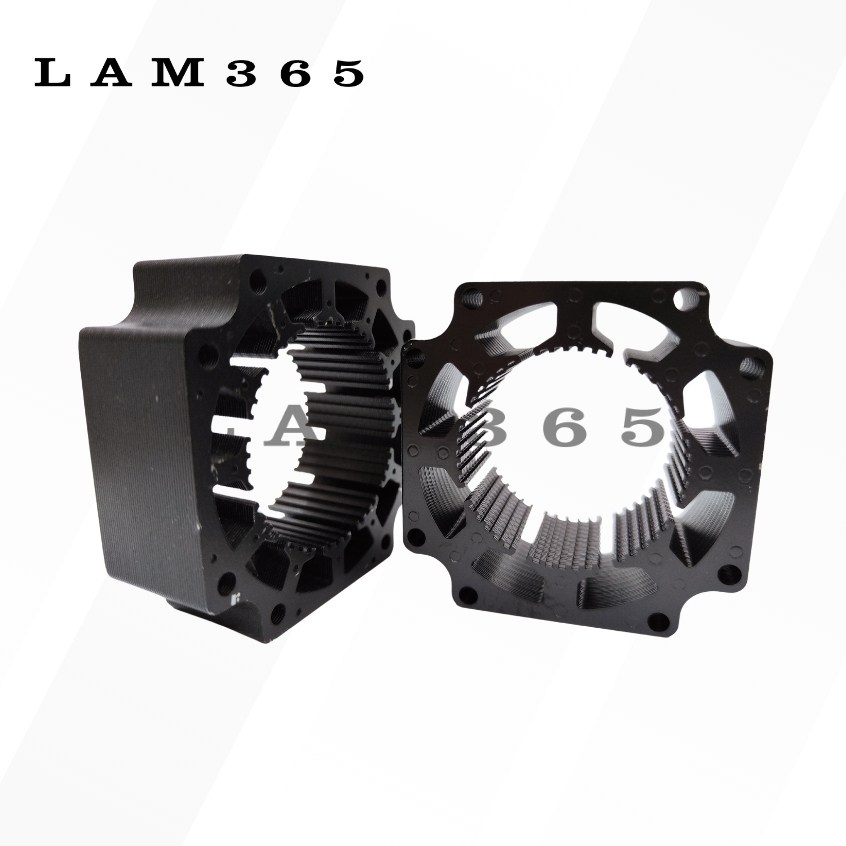
Stepper Motor Stator Core
Designed for precision and accuracy in stepper motors, ensuring smooth operation and high torque.
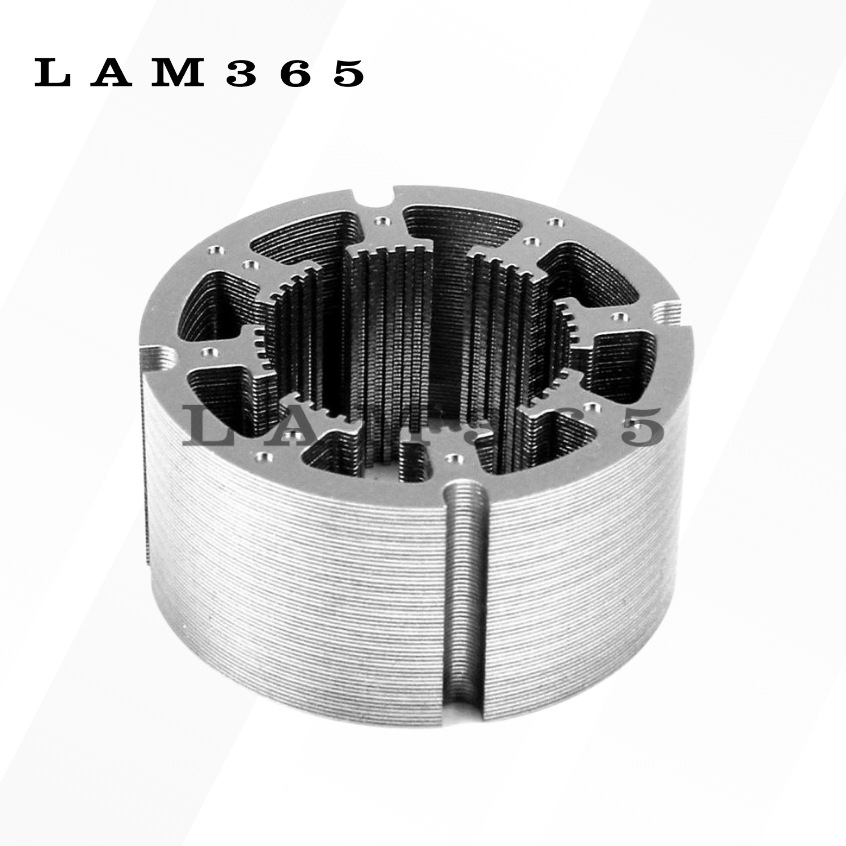
Servo Motor Stator Core
High-precision stator cores tailored for servo motors, delivering excellent control and responsiveness.
Areas of Stator Stacks Application
Stator and rotor stacks find applications across a wide range of industries, playing a crucial role in automated production lines, space and medical technology, and industrial motors.
They are essential components in pumps and power tools, contributing to efficient energy supply systems. Additionally, they are integral to heating, cooling, and air conditioning systems, ensuring optimal performance and energy efficiency.
Motor Stator lamination assemblies
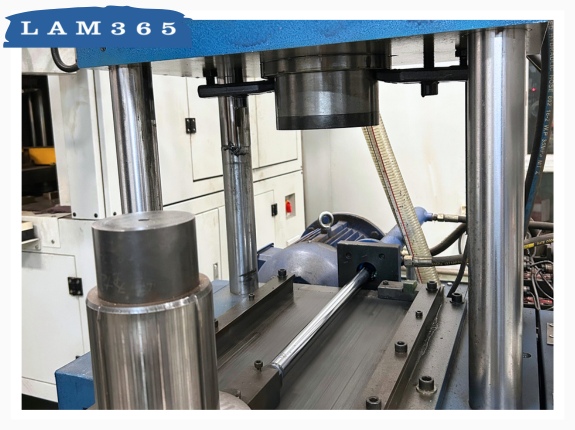
Stator Shaping
Using advanced hydraulic machines capable of applying up to 10 tons of pressure, we ensure each stator lamination is accurately formed.
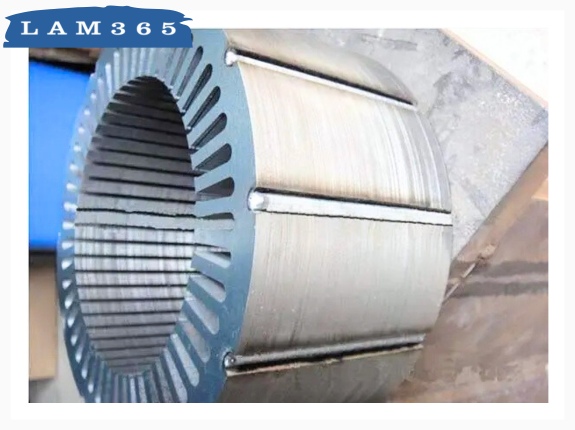
Stator lamination stacking method
We employ 4 stacking methods to assemble the laminations, including laser welding, interlocking, cleating, and riveting.
Other Processes for Motor Stator Lamination Stacks
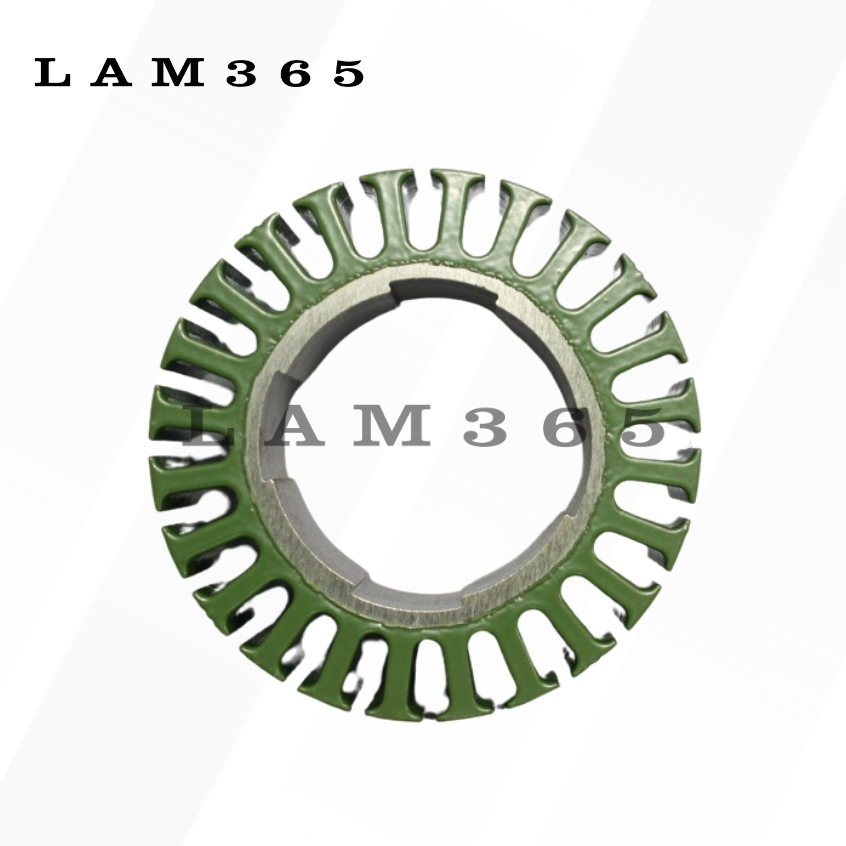
Epoxy Powder Coating
Epoxy Powder Coating involves applying a protective epoxy powder to the stator core, which is then cured to form a tough, insulating layer. This coating improves corrosion resistance, electrical insulation, and overall durability.
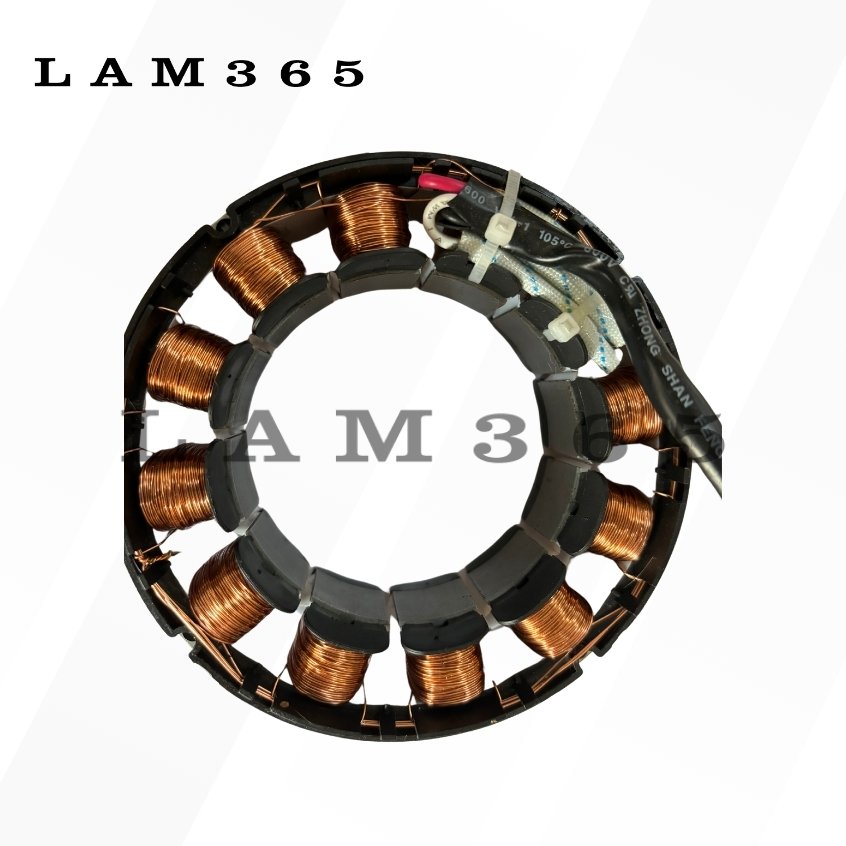
Stator Plastic Overmolding
Plastic Overmolding is another technique where stator cores are encapsulated with high-performance plastic. This process enhances mechanical protection and electrical insulation, while also reducing noise and vibration during motor operation.
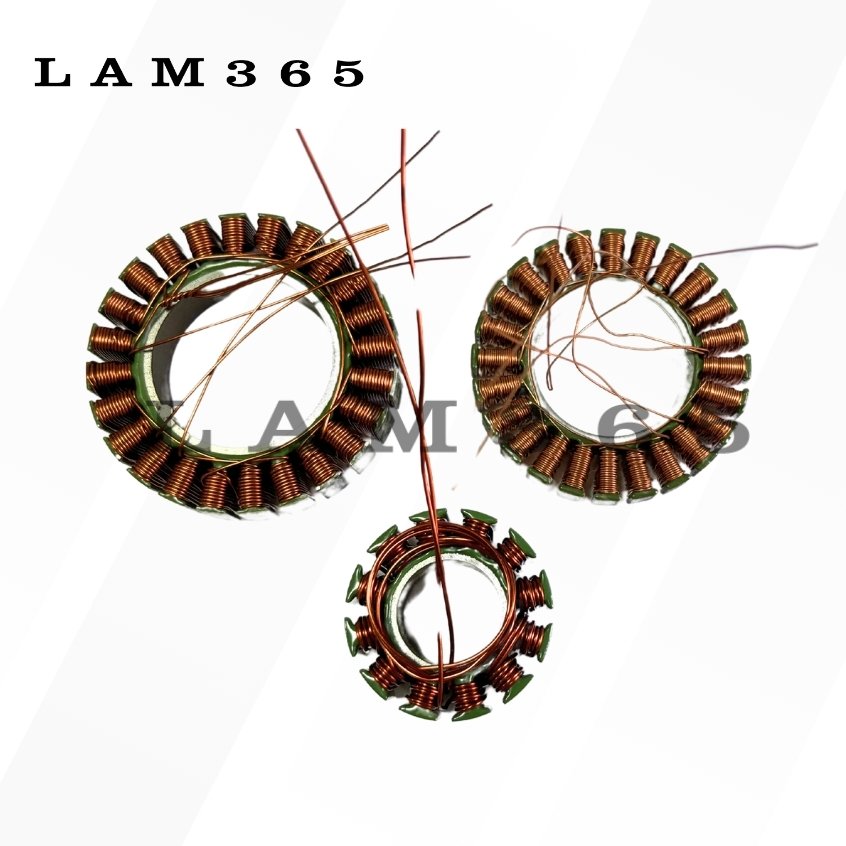
Stator Winding involves precisely winding copper wire around the stator laminations to create the electromagnetic field necessary for motor operation. Our winding process ensures optimal electrical performance, efficiency, and reliability for various motor applications.
FAQs
Stator laminations can be joined together using various methods depending on the application requirements.
They can be interlocked, where laminations are designed to fit together securely. Laser welding provides a strong and seamless bond.
Adhesive bonding offers flexibility and reduces mechanical stress.
Cleating involves bending small tabs to hold the laminations, while riveting uses metal pins for a robust assembly.
The rotor and stator are essential components of electric motors and generators. The stator is the stationary part that contains the winding or coils, which generate a magnetic field.
The rotor, on the other hand, is the moving part that rotates within the stator. It interacts with the magnetic field produced by the stator to create motion or electrical energy.
The thickness of stator lamination varies based on the application. For 50 Hz transformers, silicon steel lamination thickness typically ranges from 0.25 to 0.5mm. For 60 Hz transformers, it ranges between 0.17 and 0.27mm.
We offer custom stator laminations with thicknesses ranging from 0.1 to 0.5mm, using high-quality electrical steel to meet different performance requirements.
Stator lamination stacks are typically made from various grades of electrical steel, chosen for their magnetic properties and efficiency.
Common types include non-oriented electrical steel, which is used for general applications, and grain-oriented electrical steel, which is optimized for high-efficiency transformers and motors.
These materials are selected based on their ability to minimize energy losses and enhance the performance of the motor or generator.
Looking for Motor Stator Laminations China Manufacturer?
If you need high-quality motor rotor and stator laminations, Lam365 is the best choice. As a leading manufacturer in China, we specialize in customizing stator cores for various generator and motor types and applications.
Our advanced manufacturing processes ensure precision, durability, and optimal performance. Whether you need motor lamination stacks, self-bonding stator cores, or specialized winding services, we have the expertise to meet your requirements.