Drone Motor Lamination in China
Open Public Mold for Drone Motor Core
We have dozens of existing drone stator punching tools available. Our capabilities include:
- Electrical Steel Lamination Thickness: 0.2mm / 0.35mm / 0.5mm
- Electrical Steel Grade: TBD
- Stator Thickness: 2-200mm (customizable)
- Stator Outer Diameter: 10-250mm (customizable)
- Stator Inner Diameter: 2.8-180mm (customizable)
- Epoxy Coating Color: Green / Blue
- Mold Type: High speed progressive stamping for stator and rotor, single mold for stator and rotor
- Stacking: Interlocking
Our extensive inventory of public molds allows us to quickly meet various customization needs for drone motor cores, ensuring high-quality and efficient production.
Items | Dimension | Solts | Lamination Thickness |
---|---|---|---|
1 | Φ13.00*Φ5.80 | 9/12 slots | 0.2mm |
2 | Φ18.00*Φ6.00/8.00 | 12 slots | 0.2mm |
3 | Φ18.00*Φ9.00 | 12 slots | 0.2mm |
4 | Φ18.20*Φ8.00 | 9 slots | 0.2mm |
5 | Φ19.00*∅2.30 | 5 slots | 0.2mm |
6 | Φ20.00*Φ9.00 | 12 slots | 0.2mm |
7 | Φ20.20*Φ8.00 | 9 slots | 0.35mm |
8 | Φ22.00*∅10.00 | 12 slots | 0.35mm |
9 | Φ22.00*∅9.50 | 12 slots | 0.35mm |
10 | Φ22.00*Φ8.00 (Φ9.00、Φ9.50、Φ10.00) | 12 slots | 0.2/0.35MM |
This is only a small selection of existing standard drone stator specifications, if you would like to know more, please contact us.
Customize Motor Stator and Rotor Cores for Drone Motor
We are dedicated to sharing this expertise with our clients, helping to solve most technical issues related to drone stators and motors. Whether you need customized specifications or standard specifications for drone motor laminations, we can provide high-quality, precise, and efficient solutions.
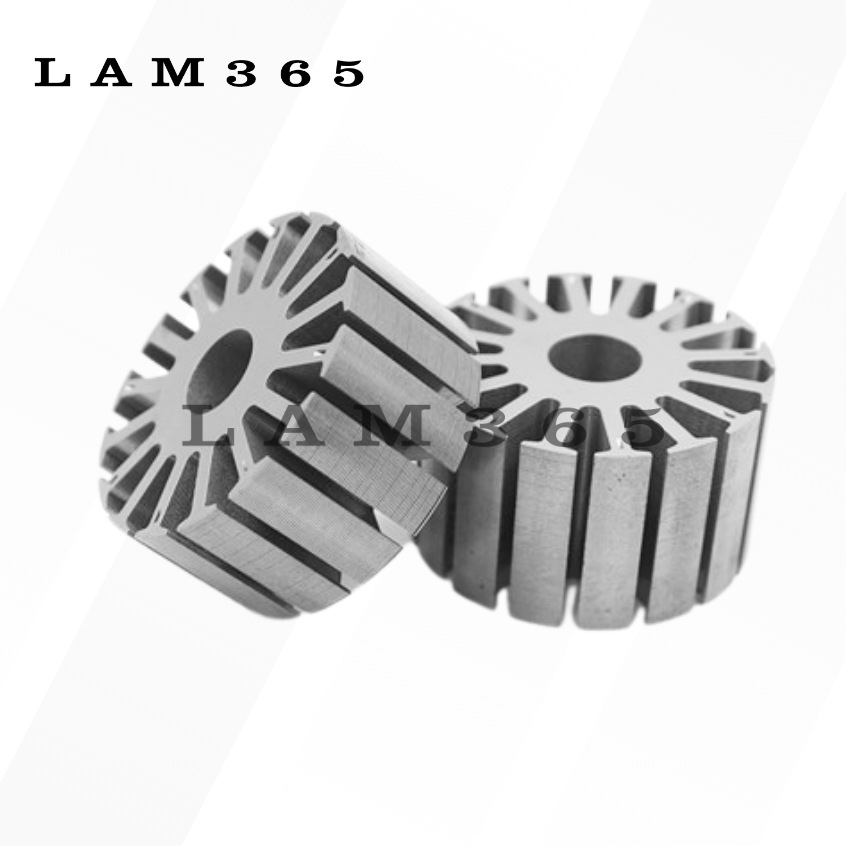
outer rotor core lamination
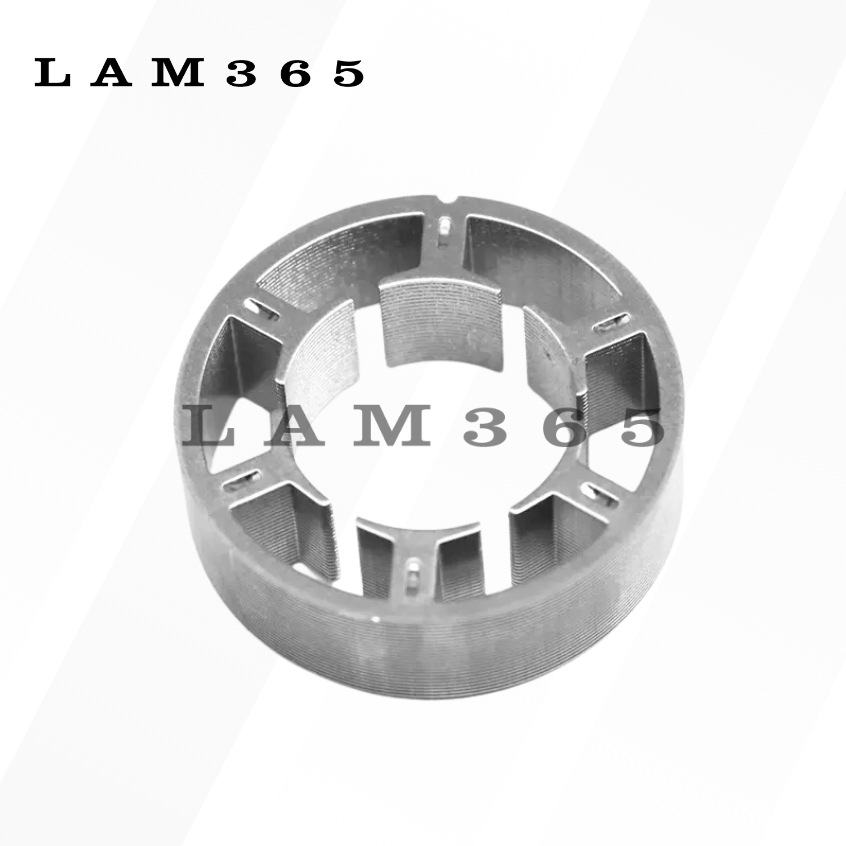
6 slots inner rotor core lamination
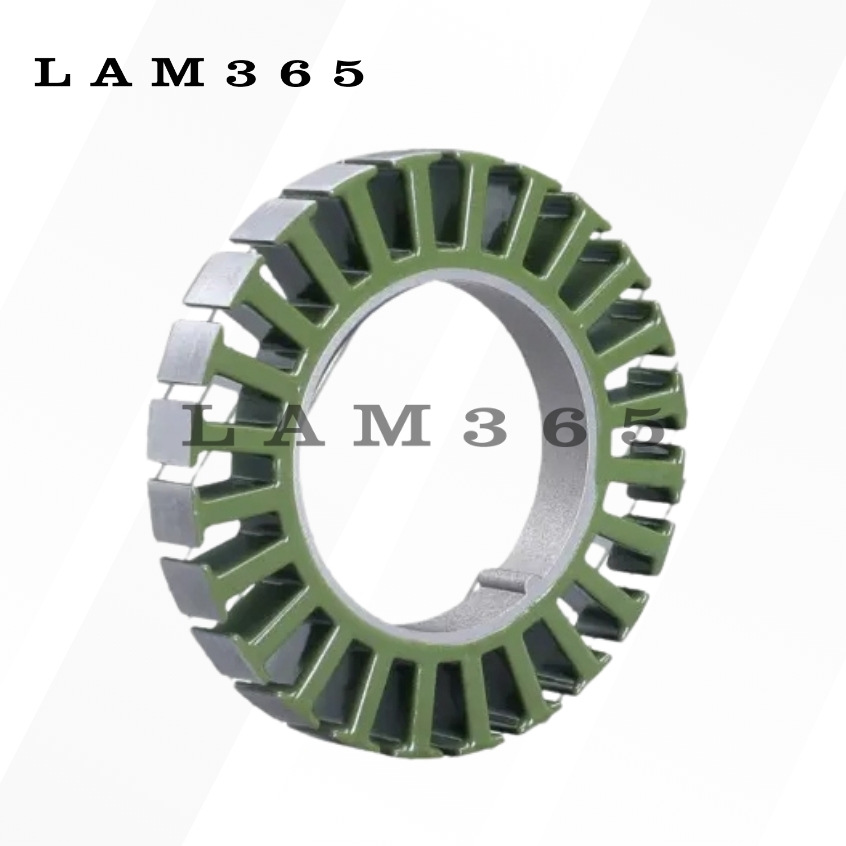
24 slots BLDC motor stator core for UVA motor
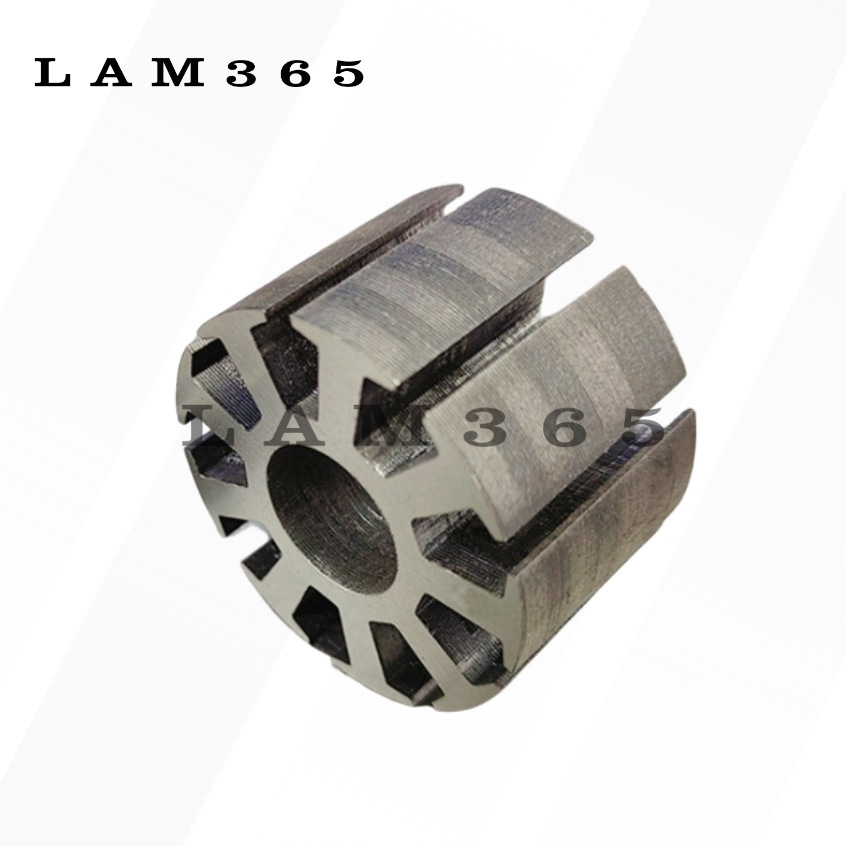
Bonding motor lamination for drone
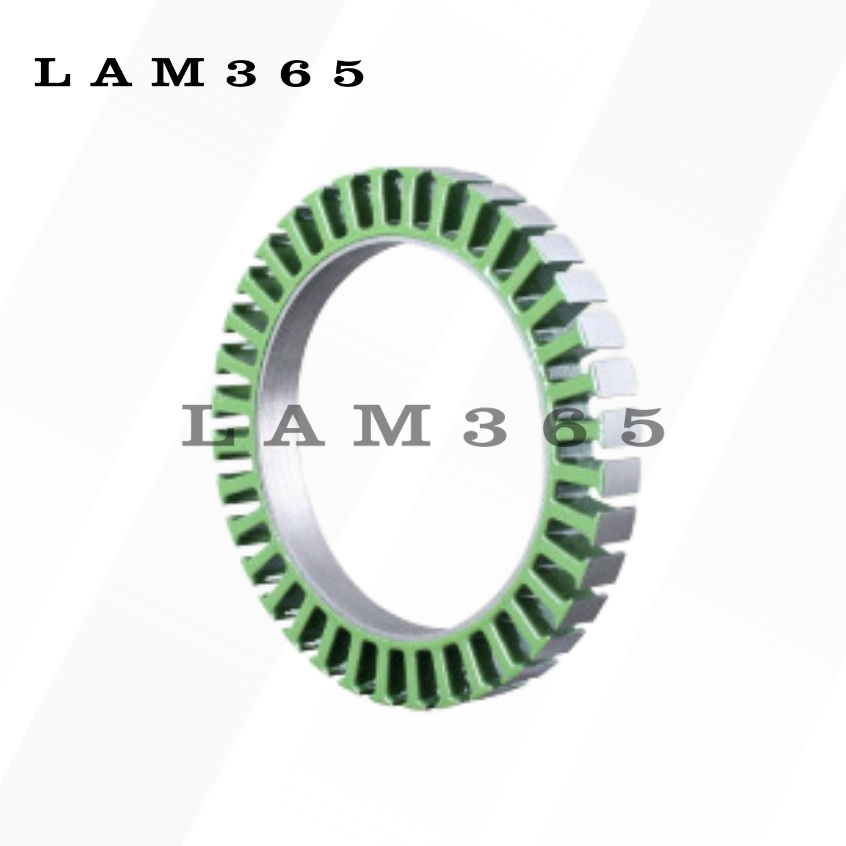
36 slots BLDC motor stator for drone motor
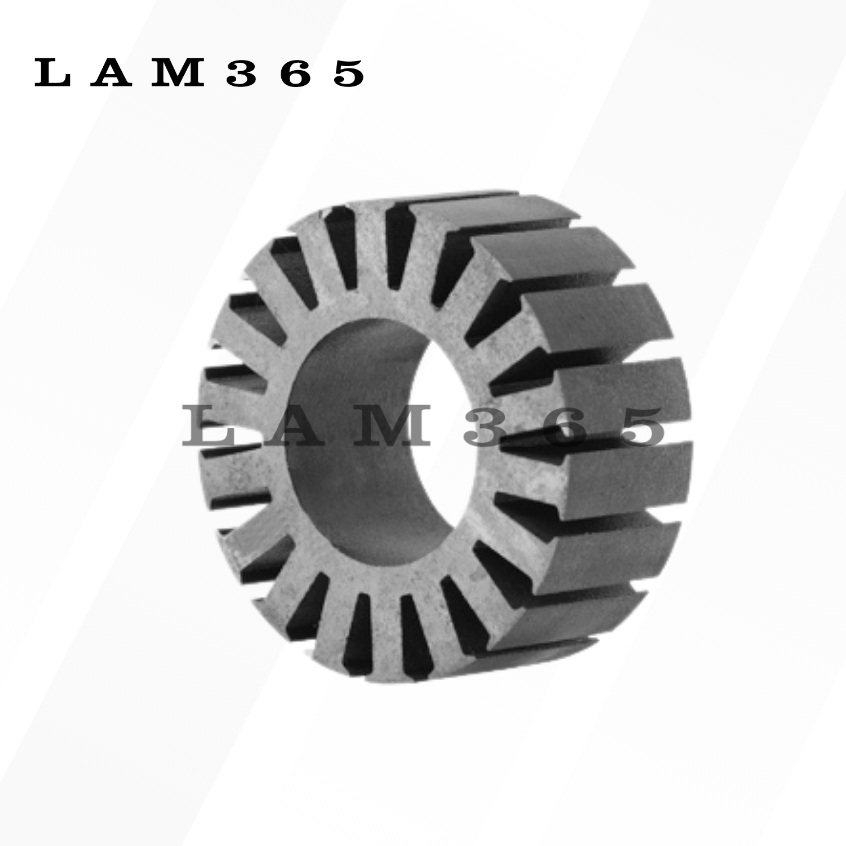
Amorphous Alloy Motor Core for drone motor
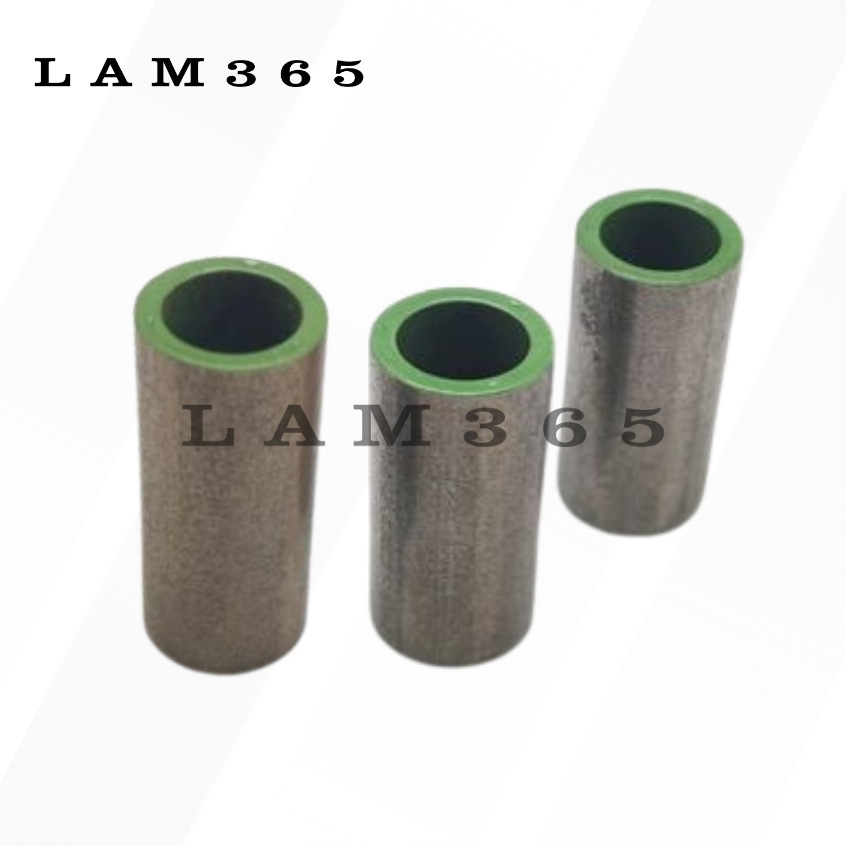
Coreless motor core for model airplane motor
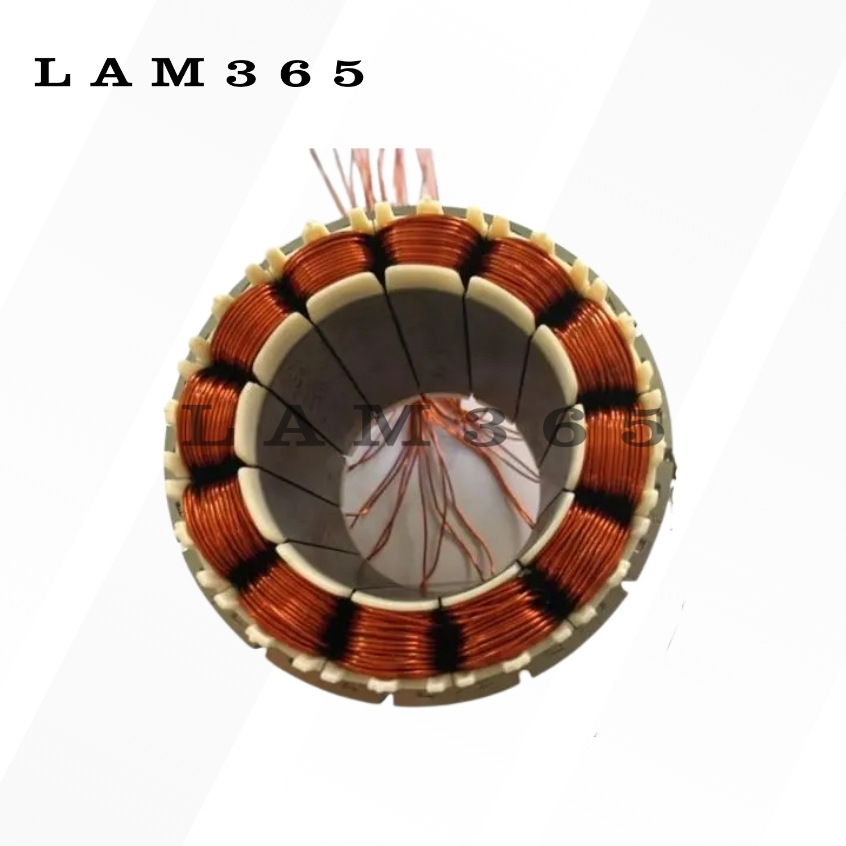
Brushless motor stator winding
Epoxy Coating Process for Drone Motor Lamination Stacks
During UVA motor operation, the UVA stator often faces oxidation, corrosion, and other impacts that can affect performance and lifespan. The stator coating process involves applying a corrosion-resistant and wear-resistant layer on the stator surface to prevent oxidation, corrosion, and mechanical wear.
We typically use epoxy resin as the coating material. The thickness is controlled between 0.20-0.30mm but can be adjusted according to customer specifications. This process ensures that the stator maintains its integrity and performance over time, providing a durable and reliable solution for drone motor applications.
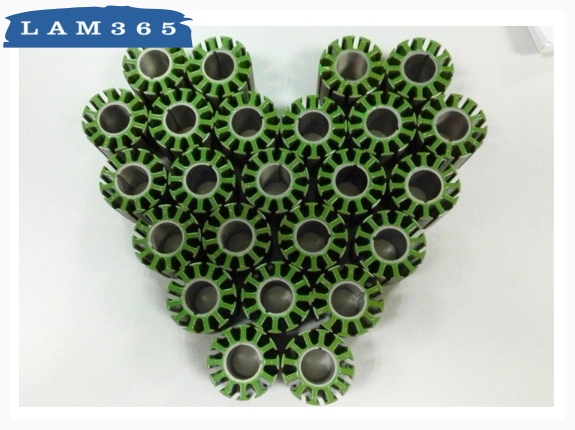
Drone Stator Winding
For drone BLDC motors, the stator slots are typically outward-facing. This structure is ideally suited for fly-fork winding, a specialized technique used for such configurations. We employ single, double, and four-position machines, offering high winding speeds and efficient production.
During the process, the winding machine uses a high-speed rotating fly fork to guide the copper wire into the stator slots precisely. The fly fork’s design ensures the wire is accurately placed, and the movement of the molding head allows for orderly winding.
This technique is characterized by its high speed and precision, making it widely applicable in model aircraft motors, balance scooter motors, skateboard motors, and electric vehicle motors.
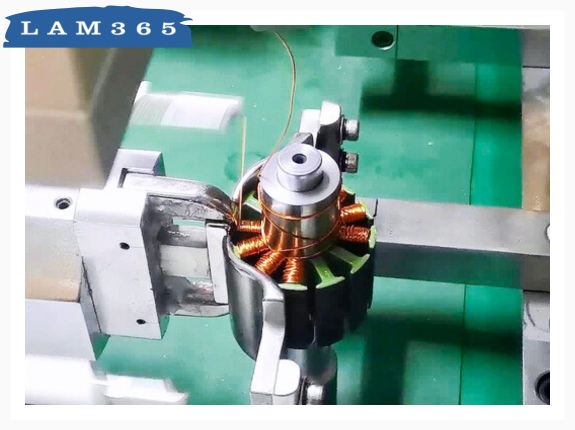
Other Products
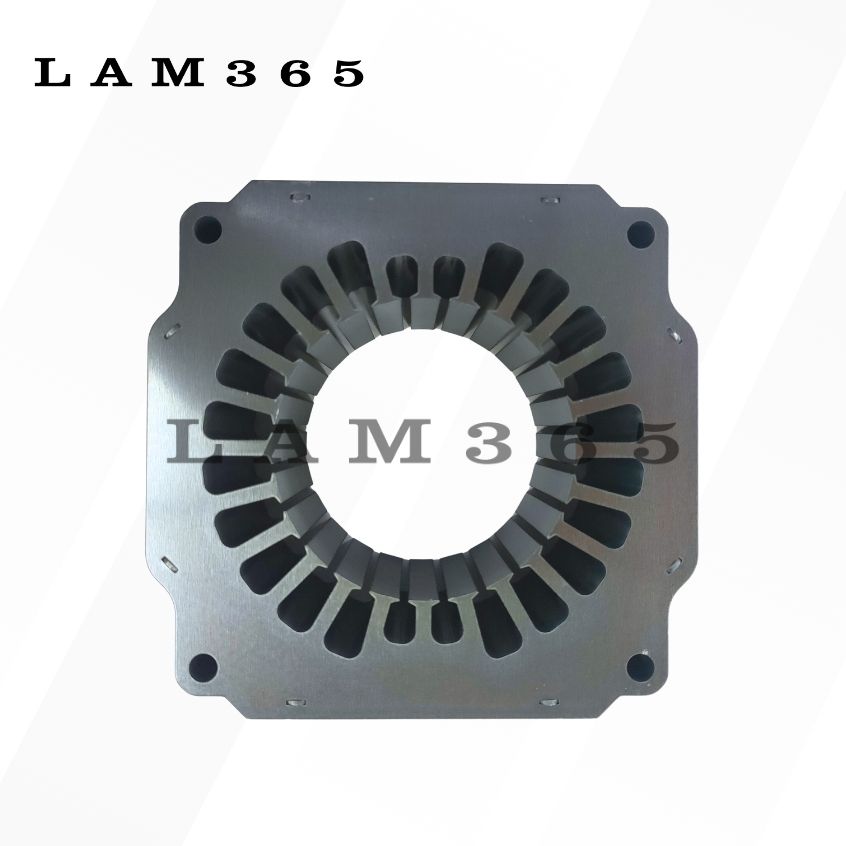
Refrigerator Compressor Motor Core
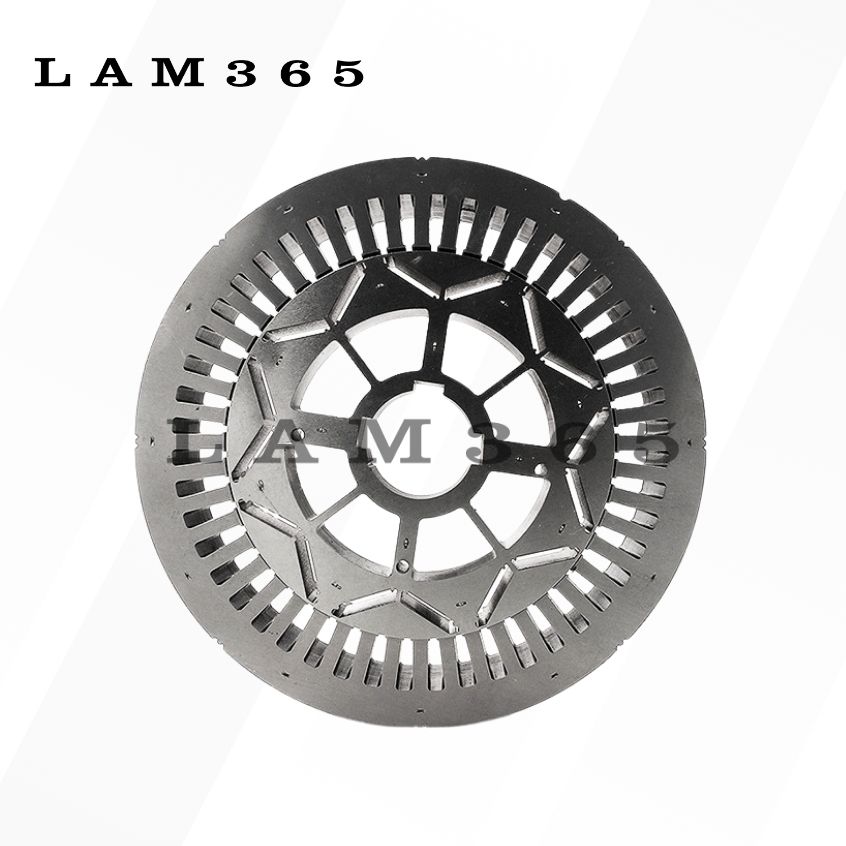
New Energy Vehicles Motor Lamination Stacks
FAQs
FPV and racing drones typically use high-performance brushless DC (BLDC) motors. These motors offer superior efficiency, high power-to-weight ratios, and rapid response times, making them ideal for the demanding maneuvers and speed requirements of FPV and racing drones.
Coreless motor cores offer several advantages for drone motors, including:
Reduced Weight: Lighter than traditional motors, enhancing drone agility and flight time.
Higher Efficiency: Minimized iron losses improve overall energy efficiency.
Smoother Operation: Lower inertia results in smoother and more responsive performance.
Improved Heat Dissipation: Enhanced cooling capabilities prevent overheating, extending motor life.
Enhanced Power Density: Provides more power in a smaller, compact design, ideal for compact drone applications.
The primary difference between an outer BLDC (Brushless DC) rotor and an inner BLDC rotor for UAV (Unmanned Aerial Vehicle) motors lies in their configurations.
In an outer rotor design, the rotor (magnets) surrounds the stator (windings), offering a higher torque due to a larger diameter and better cooling efficiency. This configuration is ideal for applications requiring more torque and stability.
Conversely, an inner rotor design places the rotor inside the stator, leading to a more compact motor with higher RPM and better dynamic response, making it suitable for high-speed applications and environments where space is limited.
Choose Us as Your Drone Motor Core China Manufacturer
Are you looking for a reliable partner for your FPV drone motor core, UAV motor stator in China? Choose us as your trusted manufacturer. With over a decade of experience and a commitment to excellence, we offer high-quality, customized solutions to meet your specific needs.
Our advanced progressive stamping technology and stator winding services ensure optimal performance and durability for your drone motors. Contact us today to discuss your requirements and experience the best in drone motor core manufacturing.