Axial Flux Motor Stator Core in China
We are a premier axial flux motor stator stacks manufacturer based in China, specializing in producing high-quality motor cores for a diverse range of applications. Most of the products are customized for high-speed, high-efficiency motors. At the same time, we can also design and manufacture molds for stamping stator rotor cores.
Axial Flux Stator Manufacturing
Lam365 focuses on disk stator process development for many years, after years of R&D investment, we have the ability of stamping and rolling, gluing, welding, polygon correction, winding, quality inspection. We can provide you with a comprehensive stator solution.
Axial Flux Stator Stamping and Rolling Process
At our manufacturing facility, we employ an advanced stamping and rolling machine to produce axial flux motor stator cores with precision and efficiency.
The stamping tooling precisely stamp the slots’ shapes and sizes in the electrical steel sheets. The stamping process is highly automated, ensuring that each slot is accurately formed to meet the specific design requirements of the axial flux motor stator.
In conjunction with the stamping process, we utilize a rolling machine system that operates synchronously with the stamping tooling. It can ensure seamless integration and coordination between the stamping and rolling processes.
The rolling machine meticulously rolls the stamped electrical steel sheets, maintaining the integrity and alignment of the slots. This is crucial for the stator’s overall performance.
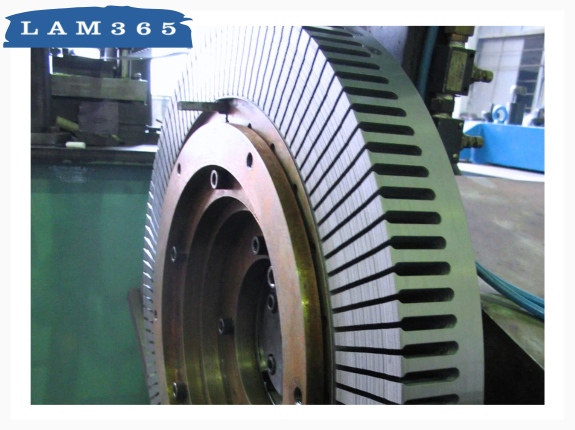
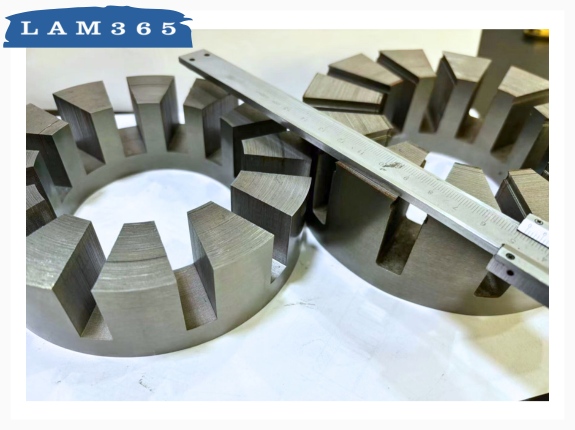
Polygon Shape Correction
The production process for the disc motor stator involves a simultaneous stamping and rolling process. During rolling, the stator core, having had its tooth material cut off, cannot adhere to the theoretical circular design. Instead, it forms a polygonal shape. Through the unique technical solution, we can realize the polygonal arc correction of the axial motor stator, so that all stator outer diameters are close to the theoretical arc shape.
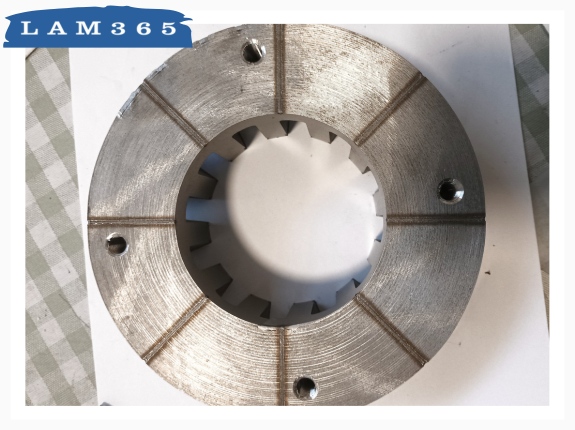
Laser Welding and Grinding
After the stamping and rolling processes, laser welding is employed to secure the stator. We use laser welding on the back of the stator to provide a fixed, durable bond. This method ensures the stator’s components are securely fastened, enhancing the overall reliability and longevity of the motor core. If necessary, we can create assembly screw holes and do surface grinding to get good flatness.
Axial Flux Stator Winding
Axial flux stator winding involves precise techniques to ensure optimal performance and efficiency. Unlike conventional radial flux motors, axial flux motors have windings placed on a flat, disc-shaped stator.
This configuration allows for a more compact and lightweight design, enhancing power density and thermal management.
For other kinds of stators, we provide two winding methods, concentrated winding and partitioned winding.
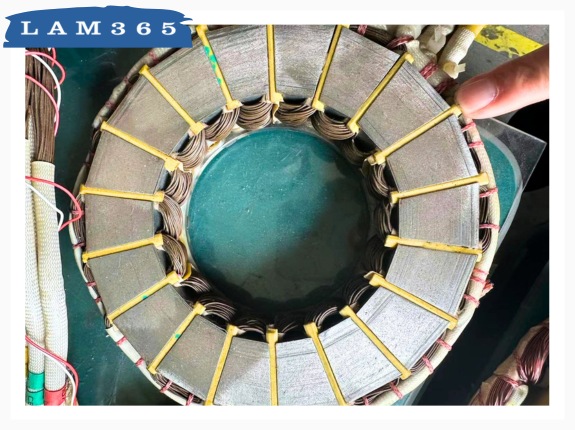
Axial Flux Stator Core Products
Our manufacturing capabilities allow us to produce customized stator cores tailored to your specific requirements, ensuring optimal performance and reliability in every product.
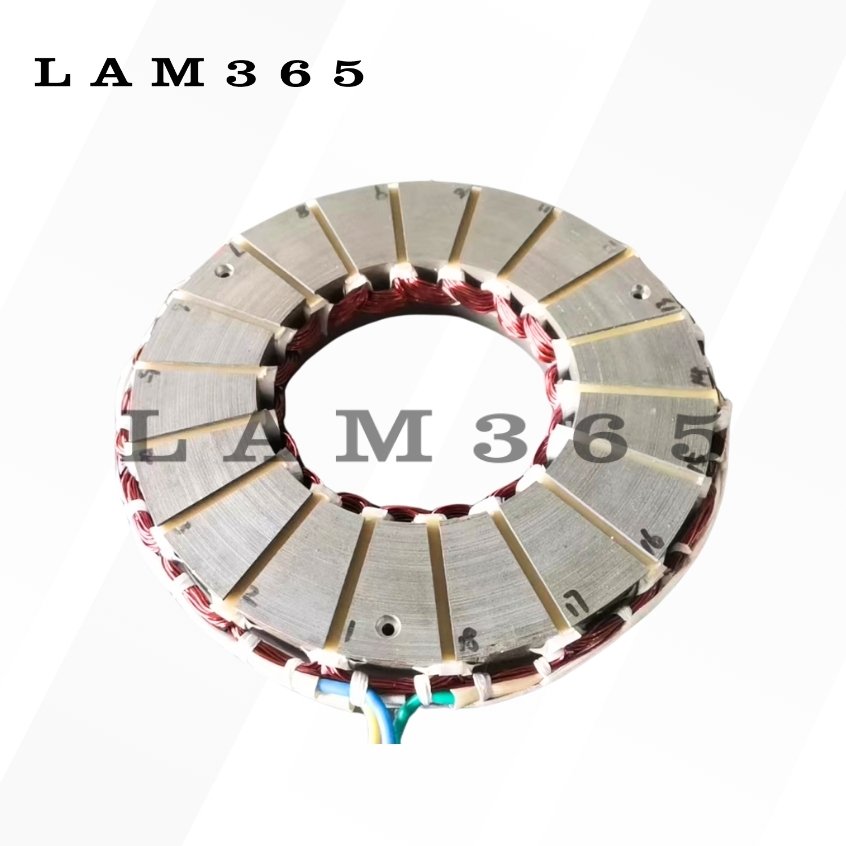
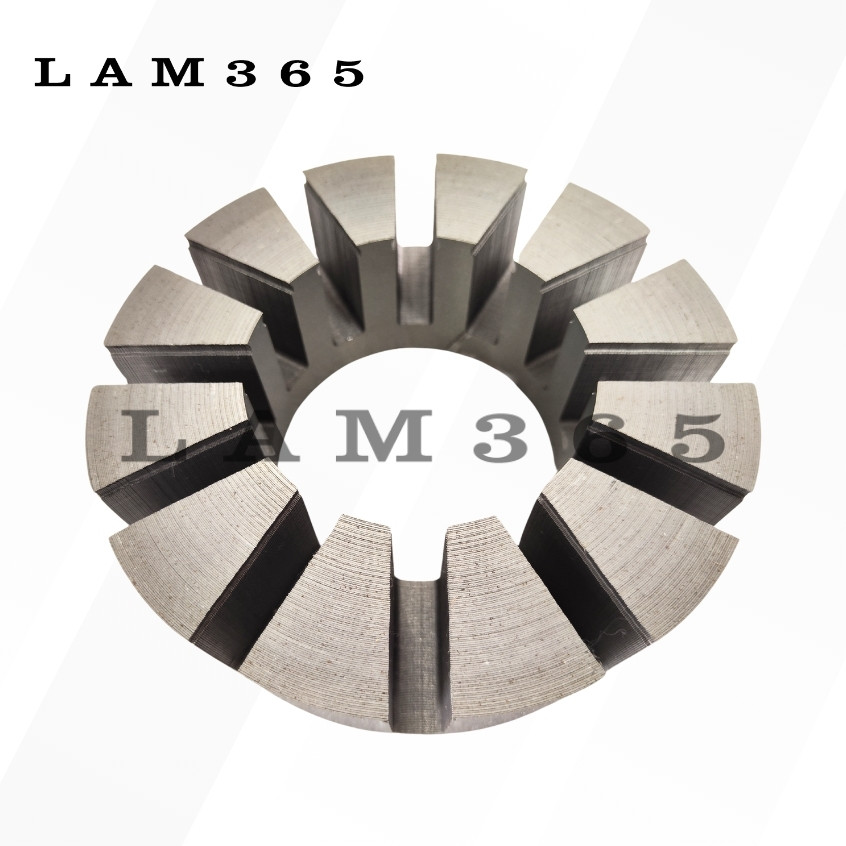
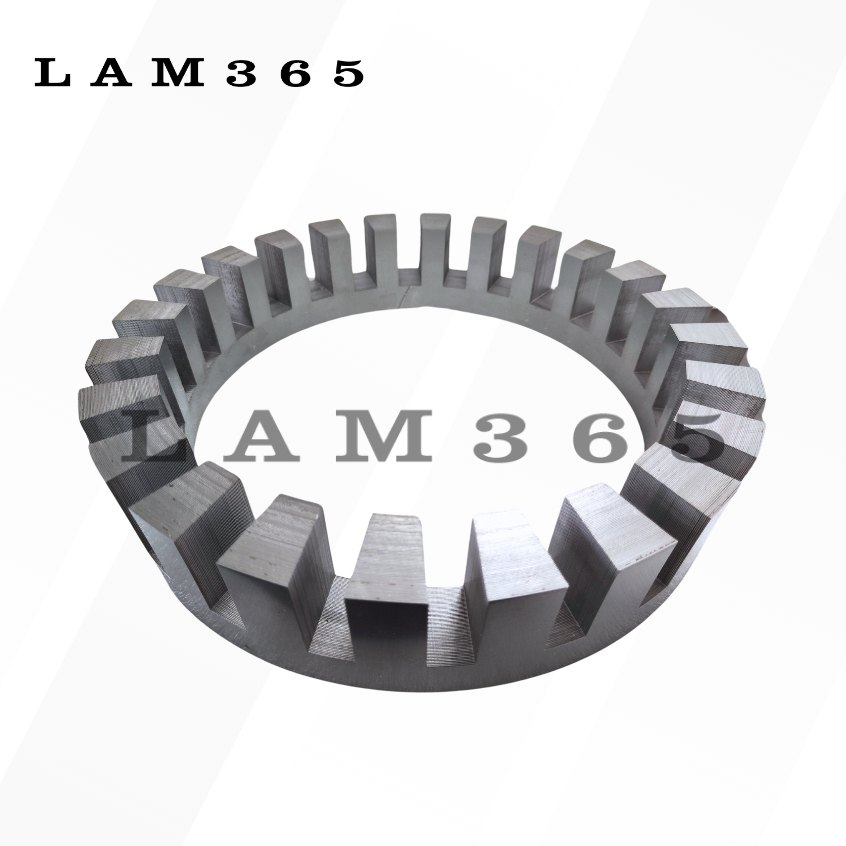
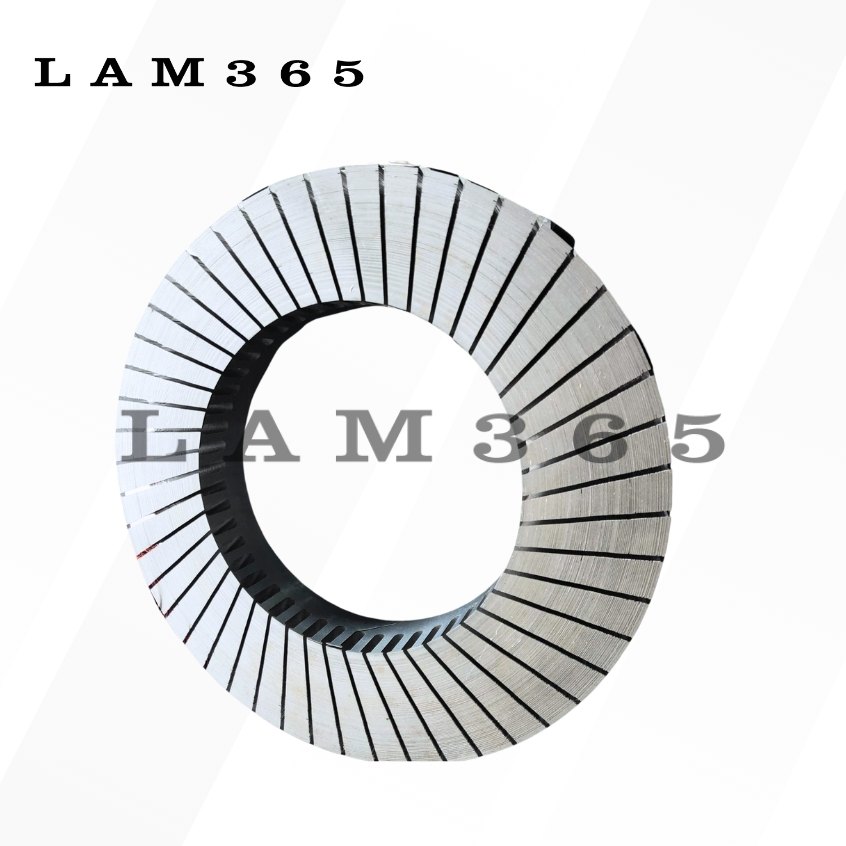
Material Selection for Axial Flux Stator Core
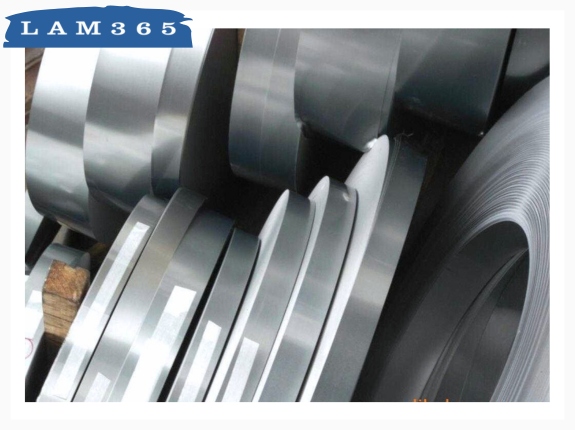
The material selection for our axial flux stator cores focuses on optimizing performance and efficiency. There are three materials, but the most common is silicon steel sheet.
Silicon Steel Sheet
Known for its excellent magnetic properties and low core loss, silicon steel is ideal for reducing energy consumption and improving motor efficiency. We can provide various grades of electrical steel, such as Baosteel, M19, M235-35A, and more.
Amorphous Alloys
These materials offer superior magnetic performance with minimal energy loss, making them perfect for high-efficiency motors and EV motors.
Soft Magnetic Materials
Soft magnetic materials are crucial for achieving high magnetic permeability and low coercivity. It can ensure the stator core performs optimally under various operating conditions.
Benefits of Axial Flux Motor
High Power and High Torque
Axial flux electric motors deliver superior power density and torque compared to conventional radial flux motors, making them ideal for high-performance applications.
Lightweight
The motor length is significantly shorter, typically 5 to 8 times shorter than traditional motors. Weight is reduced by 2 to 5 times, contributing to lighter overall system designs.
reduces material costs
Axial flux technology uses fewer materials, such as copper, iron and permanent magnets, which greatly reduces material costs and makes products more environmentally sustainable.
Improved Thermal Management
Enhanced thermal management capabilities due to the motor's flat design, which helps in dissipating heat more effectively.
Compact Design
The unique disc-shaped structure allows for more compact and space-saving installations, beneficial in applications with limited space.
High Efficiency
These motors achieve efficiency levels typically over 96%, resulting in reduced energy consumption and lower operational costs.
Other Products
FAQs
Axial flux stator cores are widely used in various applications, including electric vehicles (EVs), wind turbines, drone motor, hub motor and aerospace systems. Their compact and lightweight design makes them ideal for high-performance, space-constrained environments.
Additionally, their high efficiency and excellent torque density make them suitable for applications requiring superior energy efficiency and performance.
Despite their advantages, axial flux motors are less popular due to higher manufacturing costs and complexity compared to traditional radial flux motors. The specialized design and production techniques required can be more challenging and expensive, limiting their widespread adoption.
However, as technology advances and costs decrease, axial flux motors are becoming more viable for various applications.
The primary difference between axial and radial stators lies in their design and orientation. In an axial flux motor, the stator and rotor are arranged parallel to each other, resulting in a disc-like shape.
In contrast, a radial flux motor has a cylindrical design with the stator surrounding the rotor. This structural difference impacts the motor’s performance characteristics, efficiency, and application suitability.
Axial flux motors are significant for electric vehicles (EVs) due to their compact size, lightweight design, and high efficiency.
These motors provide excellent torque density, which enhances vehicle performance while reducing weight and space requirements.
Their efficiency leads to longer driving ranges and better energy utilization, making them highly advantageous for modern EVs.
Contact Us for Your Axial Flux Motor Stator Lamination Needs
Ready to take your motor performance to the next level with our expertly crafted axial stator cores? Contact us today to discuss your specific requirements and discover how we can meet your axial flux motor stator design and manufacturing needs.
Our dedicated support team is here to provide you with personalized service, detailed quotes, and comprehensive solutions.