Are you a motor enthusiast or a motor manufacturer looking to stay ahead of the game? Well, buckle up and get ready to dive into the world of YASA Axial Flux Motor Technology! This cutting-edge technology is revolutionizing the way we think about electric motors, offering increased efficiency, power density, and performance in a compact package. And the motors are much smaller and lighter than the radial flux motors present in almost all modern EV cars.
In this blog post, we’ll break down everything you need to know about YASA axial flux motors. From how they work their magic to the benefits they bring to the table, we’ve got you covered.
So, sit back, relax, and let’s explore this innovative technology together.
History and Development of YASA
YASA, founded in 2009, is a British motor company and an important player in high-density axial-flux motors. It is more famous than Equitmake.
It is worth mentioning the origin of its name. “YASA” is actually the abbreviation of a special axial magnetic field motor technology. The full name is ‘Yokeless And Segmented Armature’, which means a stator winding core technology with segmented and yokeless parts.
Founded in 2009, YASA (Yokeless And Segmented Armature) aimed to create a more efficient, compact, and powerful motor. The journey started with developing a unique axial flux motor that eliminated the need for a traditional yoke, resulting in a lighter and more efficient design.
Over the years, YASA’s innovative approach led to significant milestones. Early prototypes demonstrated superior power density and efficiency, attracting attention from the automotive and aerospace industries.
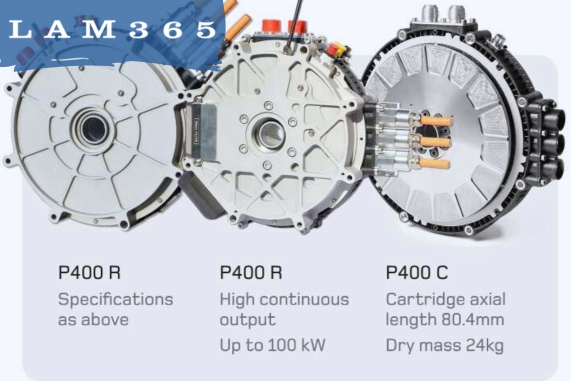
By 2012, YASA motors were integrated into high-performance electric vehicles, showcasing their potential in real-world applications. They have launched a series of amazing motor products. P400S can achieve a peak torque density of 15.4Nm/kg and a peak power density of 6.7kw/kg. And P750, because of its larger size, has a torque density of 21.4Nm/kg and a power density of d5.4kw/kg.
5 Key Technologies of YASA Axial Flux Motor
1. Axial Magnetic Field Topology: Rotor-Stator-Rotor Configuration (Double Rotor Single Stator)
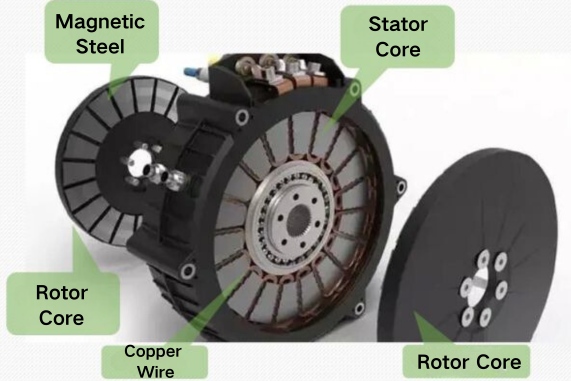
The YASA axial flux motor utilizes an advanced Rotor-Stator-Rotor (R-S-R) configuration. Unlike traditional radial motors, where torque is proportional to the motor’s volume, axial flux motors benefit from a torque that scales with the cube of the motor’s outer diameter. This results in significantly higher torque in designs where the diameter (D) greatly exceeds the length (L).
In the R-S-R setup, a single stator is sandwiched between two rotors. This design eliminates the need for a bulky stator yoke, reducing weight and allowing for a more compact motor. The absence of the yoke also minimizes iron losses, enhancing efficiency. Additionally, placing the rotors on both sides of the stator allows for the use of more magnetic material, substantially increasing torque density.
2. Yokeless and Segmented Armature
The YASA axial flux motor’s name derives from its groundbreaking “Yokeless and Segmented Armature” technology. To understand its advantages, it’s helpful to compare it to traditional designs. Conventional stators have a yoke—a structural component connecting all stator teeth and serving as a magnetic path to complete the magnetic circuit.
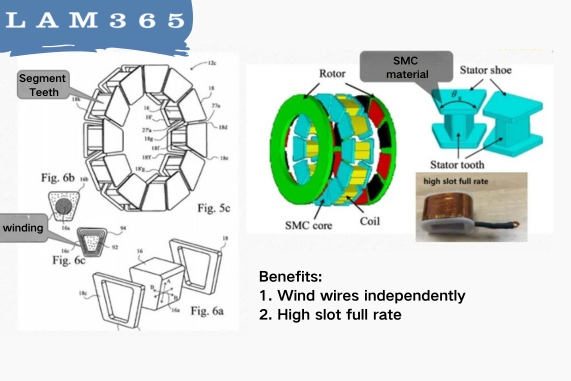
In contrast, YASA’s design eliminates the stator yoke. Each stator tooth operates independently, allowing the magnetic field to traverse directly from one side of the tooth to the other, closing the loop through the rotor. This yokeless design offers several significant benefits.
First, without the stator yoke, issues like magnetic saturation and associated losses are minimized, enhancing efficiency and enabling a more compact motor design. The segmented structure allows each winding to be pre-wound and then assembled, facilitating large-scale automated production.
Second, the independent winding of each segment allows for optimal space utilization through precise wire placement, achieving high slot fill rates. Higher slot fill rates mean more copper can be packed into the same space, reducing copper losses and further increasing torque density.
Overall, the yokeless and segmented armature design of YASA motors enables higher efficiency, reduced weight, and improved manufacturability, making it a cornerstone of their advanced motor technology.
3. Tooth Integration Technique
In YASA’s axial flux technology, each tooth operates independently but must transmit electromagnetic force precisely positioned between two rotors. The challenge of positioning and securing these teeth is ingeniously addressed through YASA’s patented “Clam Shells” structure.
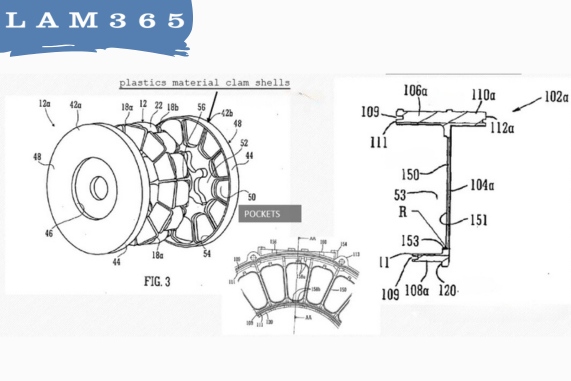
This technique involves a plastic support structure, known as the fixed plate or “Clam Shells,” which houses multiple pockets. Each pocket holds a stator tooth, ensuring precise positioning and secure fastening. The outer wall of the fixed plate integrates with the motor housing, while the inner wall aligns with the bearing chamber, providing robust structural support.
This innovative tooth integration technique not only ensures high precision and stability but also contributes to the overall efficiency and reliability of YASA axial flux motors.
4. Flat Wire Winding
A standout feature of YASA axial flux motors is the use of flat wire winding technology. Unlike traditional round wire windings, YASA employs extremely flat copper wires wound in precise layers. This technique, enabled by advancements in automation, allows for highly efficient and compact winding assemblies.
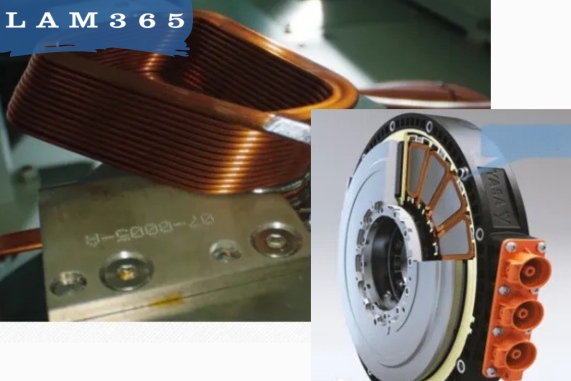
The flat wires are grouped and installed on the stator teeth, with their ends connected via busbars. This method significantly increases the slot fill rate, achieving over 60% net copper slot fill. Higher slot fill rates mean more copper within the same space, which enhances torque density and overall motor performance.
The combination of flat wire winding and YASA’s unique technology boosts the motor’s efficiency, making it more powerful and compact, ideal for high-performance applications.
5. Oil-Cooled Design
The YASA axial flux motor incorporates an advanced oil-cooled design that significantly enhances its performance. The cooling system features an annular oil channel with two flow paths: one moving counterclockwise and the other clockwise. This dual-path flow ensures that every flat wire winding is fully enveloped by the cooling oil.

The design adds additional structures to the fixed plate, creating a circular flow path for the oil. Compared to conventional oil-cooled motors, this method is more efficient as it cools both the windings and the stator teeth simultaneously. Each tooth and winding has multiple surfaces in contact with the cooling oil, maximizing the heat exchange area.
This efficient oil-cooling structure substantially boosts torque density by maintaining optimal operating temperatures, ensuring the motor’s performance and longevity in high-demand applications.
Conclusion
In summary, YASA axial flux electric motors stand out due to their innovative Rotor-Stator-Rotor configuration, yokeless and segmented armature, precise tooth integration, flat wire winding, and efficient oil-cooled design. These technologies work together to deliver high power and torque density, improved efficiency, and compactness, making them ideal for new energy vehicles, and new energy aircraft applications.
Ready to harness the power of axial flux motor technology for your electric car projects? Contact us today to discuss custom axial flux motor stator solutions tailored to your needs. Let’s transform your ideas into high-performance reality!