Have you ever wondered why two motors of the same specifications can perform so differently, with one running smoothly while the other tends to overheat? The answer might lie in the slot fill factor.
As an experienced motor stator core China manufacturer, I know that the slot fill factor plays a crucial role in determining motor performance. It affects not only the motor’s efficiency but also its lifespan and reliability.
In this blog, we’ll delve into what slot fill factor is, how it impacts motor performance, and how optimizing it can enhance the overall quality of electric motors. Whether you’re an engineer or simply interested in motor technology, read on to uncover the importance of this often underestimated factor.
What is Slot Fill Factor?
The slot fill factor is a key parameter in motor design that describes how effectively the winding coils fill the space within the stator slots. Specifically, it represents the ratio of the space occupied by the winding coils to the total slot space.
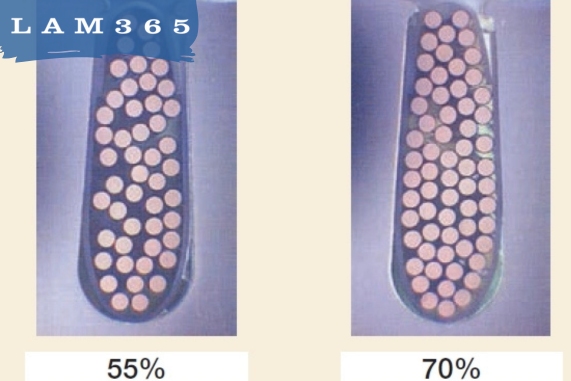
In a motor, the stator slots need to be designed to ensure that the winding coils can effectively fill the space in the slots. A higher slot fill ratio means that more winding coils can be placed in each slot, thereby improving the power density and efficiency of the motor. A lower slot fill ratio may lead to reduced efficiency and overheating problems in the motor.
The slot fill ratio directly affects the performance and reliability of the motor because it is related to the motor’s thermal management and the ability of current to pass through the windings. Optimizing the slot fill ratio can improve the energy efficiency and working stability of the motor.
How to Calculate the Slot Filling Factor?
Since there are many gaps between the copper wires in round wire winding motors and the paint film accounts for a large proportion, the pure copper slot fill rate is generally around 40%.
To calculate the slot filling factor, follow this formula:
Slot Fill Factor=Total Cross-Sectional Area of Windings/Cross Sectional Area of Stator Slot
1. Measure the total cross-sectional area of the windings within the slot.
2. Measure the cross-sectional area of the stator slot.
3. Divide the area of the windings by the area of the slot.
This ratio provides the slot-filling factor, indicating how effectively the slot space is utilized by the windings. A higher value reflects a better use of available space, impacting motor efficiency and performance.
Factors Influencing Slot Fill Factor
Several factors affect the slot fill factors, each playing a role in optimizing motor performance.
Wire Gauge: Thinner wires can fit more snugly into the slots, thereby increasing the fill factor. However, the choice of wire gauge must balance with other performance criteria.
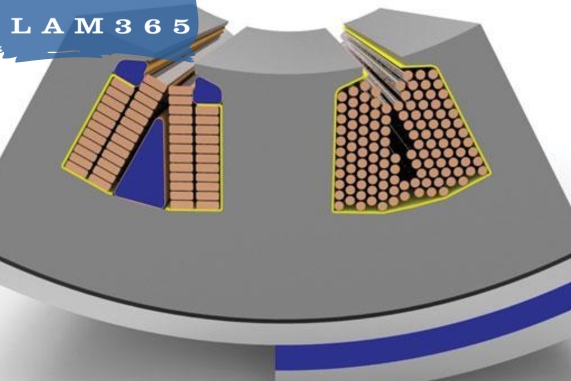
Type of Windings Used: Optimizing the winding layout can significantly improve the factor. Techniques, like layered or interleaved winding configurations, can maximize the use of available slot space.
Slot Shape and Size: The dimensions and shape of the slots impact how well the windings fill the space. Deeper and narrower slots often allow for a higher fill factor, as they accommodate more winding material.
Insulation Materials: Using thinner insulation materials can also enhance the factor. This approach allows more winding material to fit into the slots, improving overall efficiency.
By considering these factors, you can effectively increase the factor, leading to better motor performance.
How Slot Fill Factor Affects Motor Performance
The slot filling rate has a significant impact on various aspects of motor performance.
Motor Performance: A higher slot filling rate generally enhances a motor’s power density, allowing it to deliver more power within the same volume or mass. However, aiming for the highest possible fill factor is not always ideal. Excessive slot fill can lead to increased temperature rise and localized hotspots within the windings, which can negatively affect performance.
Thermal Management: High slot filling factors result in denser windings, which can impair the motor’s cooling efficiency. If the motor cannot dissipate heat effectively, temperatures can rise, reducing overall efficiency and lifespan. Balancing performance with effective cooling is crucial.
Manufacturing and Maintenance Costs: Increasing the fill rate can complicate winding processes, raising manufacturing and maintenance costs. Tighter windings may also demand higher precision and more rigorous quality control.
Motor Efficiency: Higher slot filling factors often lead to increased copper losses due to denser windings, which raise electrical resistance. In some cases, reducing the factor slightly can improve overall efficiency.
Operating Environment: Different operating conditions, such as high temperatures, altitude, or humidity, may require adjustments to the factor to ensure optimal motor performance and reliability in those environments.
Conclusion
The slot fill factor is crucial for optimizing motor performance and efficiency. By assessing factors such as wire gauge, winding arrangement, and slot dimensions, you can improve the slot fill rate and, consequently, the motor’s power density and thermal management.
For tailored solutions and custom motor cores designed to meet your specific needs, contact us today. Our expertise ensures that your motors achieve peak performance and reliability in any application.