Have you ever wondered how the winding method of a drone motor stator can significantly impact its performance? As a professional drone outer stator manufacturer with years of experience in the field, we are excited to share insights about one of the most efficient winding methods—flying fork winding.
Whether it’s enhancing motor performance or extending its lifespan, flying fork winding offers unique advantages. In this blog, we will delve into the principles, benefits, and applications of this winding method in drone motors, helping you understand why choosing flying fork winding is a smart decision. Let’s get started!
What is Flying Fork Winding?
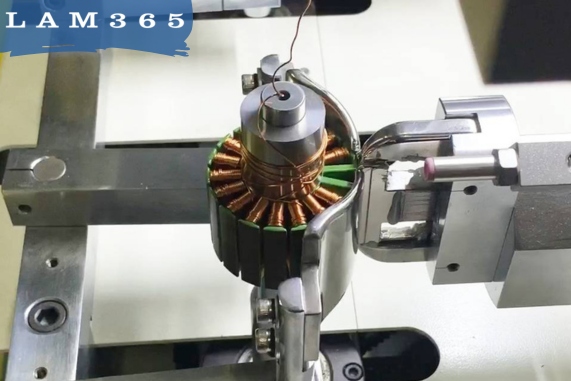
Flying fork winding is a winding method, which is characterized by the workpiece not moving, the enameled wire rotates around the workpiece and arranges the wire.
The outer winding machine uses the arc-shaped lead-in end face to slide the wire down the arc surface, and the end position is pushed by the system to the position where the coil is wound.
When the stepping screw is rotated one circle, it retreats or advances a distance of the thickness of the copper wire, and then winds another circle until it is full of a row and then changes direction.
Some friends may ask, why do we need to change direction, not one by one in sequence? In fact, the commutation is mainly for the magnetic pole pairing, otherwise the motor will not turn.
Advantages of Flying Fork Winding for Drone Motors
1. Fast Winding Speed and High Efficiency
One of the standout benefits of the winding is its impressive speed. The winding machine can achieve speeds of over 2500 rpm, making it highly efficient for various winding tasks.
2. Flexible Workstations
The machines come with single, dual, or quad workstations. This flexibility allows for tight single-wire winding or multiple wires wound simultaneously, catering to different production needs.
3. Modular Design Fixtures
The fixtures used in outer winding are designed modularly, making it easy to switch between different winding setups. This design simplifies operations and reduces downtime during changes.
4. Versatile and Quick Adjustments
The winding machines can adapt to various motor types quickly, ensuring seamless transitions between different stator cores. This adaptability is crucial for meeting diverse production requirements.
5. Customizable Winding Solutions
Outer winding machines offer non-standard customizable winding solutions for special stator cores. This capability ensures that the technique can be applied to various external stator windings, enhancing its versatility.
Overall, flying fork winding brings significant advantages in speed, flexibility, ease of use, and adaptability, making it an excellent choice for manufacturing high-performance drone motors.
Applications of Flying Fork Winding Method
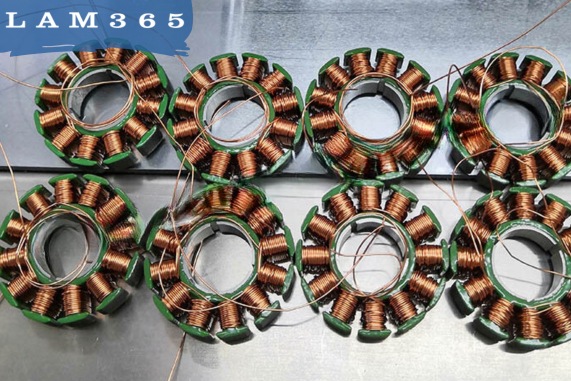
Flying fork winding is primarily used for various external outer stator windings. It is ideal for model aircraft motors, massage gun motors, balance scooter motors, electric scooter motors, new energy vehicle motors, rotary transformers, hoverboard motors, cooling fan motors, and agricultural drones.
This versatility ensures that outer winding can meet the diverse needs of modern motor manufacturing, providing efficient and reliable solutions across multiple industries.
Conclusion
Flying fork winding is a game-changer in the world of drone motor manufacturing. Its high speed, efficiency, and adaptability make it a superior choice for creating high-performance motors. Whether you’re working with model aircraft, balance scooters, or new energy vehicles, this winding technique ensures your motors run smoothly and last longer.
Curious to see how outer winding can boost your drone’s performance? Ready to take your motor manufacturing to the next level? Contact us today to customize your drone motor outer stator. Let’s elevate your drone’s efficiency and reliability together!